Let’s admit it, we lose stuff. Some studies calculated that, on average, people lose 3,000 items in their lifetime and spend about one year of their life looking for them. But if misplaced keys, wallets, or mobile phones are, well, annoying though rarely critical, losing a pallet of someone’s merchandise at your warehouse can add up to significant losses.
And that’s exactly what happens at an incredible scale globally. Companies lose 10 to 40 percent of supply chain assets annually due to misplacement, theft, or breakage.
Source: memegenerator.net
To prevent asset loss, tracking systems are implemented. Telsyte’s Asset Loss White Paper claims that businesses expect a $1.34 return on every $1 invested in such solutions – which means initial investment is offset in just 3 years. Besides just showing where things are located, advanced asset tracking systems boost efficiency (e.g., global manufacturer Stanley Black & Decker reports a 20 percent increase in productivity), support maintenance activities, and help identify optimization opportunities.
So let’s discuss what asset tracking systems are, how they work, the technologies that stand behind them, and how they benefit logistics and manufacturing companies.
What is asset tracking?
Asset tracking refers to monitoring the location and movements of such physical assets as equipment, merchandise, containers, or vehicles either by scanning barcodes or other labels attached to them or by using electronic tags that broadcast their location (GPS, RFID, etc.). Modern asset tracking systems allow business operators and managers to always be on top of their assets’ location, condition, maintenance status, and performance, having access to all collected data in centralized storage.
The same technologies can also be used to track people within the facility (mainly for security, navigation, or analytics purposes).
Asset management vs asset tracking
Asset management is a broader term that often relates to a completely different sphere and defines handling the financial assets of an individual or company and deriving value from them. In the industrial sense, asset management refers to a wide range of activities related to overseeing, operating, and maintaining the company’s physical assets (usually, equipment and machinery).
Meanwhile, asset tracking, one of the main asset management components, focuses on monitoring the movable asset's location.
Inventory tracking vs asset tracking
In a nutshell, inventory usually refers to short-term investments or goods that are held for sale or production (parts or raw materials), while assets are long-term investments or items that the company needs for operation (e.g., buildings, vehicles, equipment, tools, etc.). So inventory tracking usually means monitoring stock levels, while asset tracking relates to locating the company’s possessions.
However, in accounting, inventory is considered an asset. Besides, in terms of tracking, technologies and methods overlap, so in this post, we’ll talk about both inventory and asset tracking.
RTLS vs asset tracking
A real-time location system or RTLS is an autonomous system based on a network of connected devices that help identify and track objects by providing continuous real-time updates. That said, asset tracking in a broad sense doesn’t always entail real-time data transmission.
RTLS can be seen as one of the types of asset tracking. At the same time, asset tracking is just one of the RTLS applications, as it can also be used for on-site worker location monitoring, visitor navigation, animal tracking, and so on. Please refer to our dedicated RTLS post for more details on how these systems work.
Why implement asset tracking: main logistics challenges and problems
Evolving from monitoring the location of vehicles and railcars, today, with the development of advanced Internet of Things (IoT) technologies, asset tracking offers vast opportunities as it provides great visibility into tons of important asset-related information. Let’s look at some common logistics industry challenges that technology-based tracking can help cope with.
Asset/inventory/tool misplacement. We’re not talking about the average annual number of 1,582 containers lost at sea since asset tracking doesn’t prevent hurricanes (yet). But the common logistics problem is just not knowing where exactly assets are at any given moment, whether it's eCommerce packages in the distribution center, tools in the manufacturing facility, or handling equipment in the yard. The attached tracking devices can help immediately locate and identify assets, saving time and effort.
The reasons why assets can’t be found. Source: Telsyte’s Asset Loss White Paper
Inefficient inventory management. Manual inventory counts take too long and are too error-prone. Scanning tags and having all the information automatically transferred to the business management system is way more effective, accurate, and faster.
Theft. Both internal shrinkage and shoplifting are almost unavoidable, especially if no protective measures are taken. To get an idea of the scale, retail shrink now reaches almost $100 billion, as reported in the 2022 National Retail Federation’s Security Survey. And it’s not only about shoplifting small items: Even forklifts get stolen! Vehicle theft resulted in over $7 billion in losses in 2020.
The adoption of asset tracking technologies helps address theft at all stages of the supply chain, from manufacturing to last-mile delivery. In many cases, it involves geofencing – setting up virtual zones and receiving automatic alerts when a tagged item leaves the designated zone.
Just another way to prevent theft. Source: imgflip
Asset breakage and downtime. Unexpected equipment failure disrupts operations and causes costly downtime. Smart, sensor-equipped tags allow operators to monitor equipment health, get alerts about potential breakages, and proactively plan maintenance activities. Check our article to know more about how predictive maintenance works.
Complicated compliance and insurance procedures. In some industries (e.g., food, pharmaceuticals, or military goods production), there are strict regulations and compliance requirements. Asset tracking and accurate condition monitoring are indispensable parts of compliance procedures, so automation facilitates these processes as well. Plus, asset tracking is required for insurance purposes.
Lack of visibility into operations. Having all asset- or inventory-related data in one place is vital for getting a complete picture of the business workflows. This way, managers can analyze operations and performance and find areas for improvement, for example, detect underutilized machinery or optimize routes in a warehouse/yard/terminal by monitoring handling equipment trajectories.
If properly chosen and implemented, asset tracking technologies help transform poorly organized companies into agile, well-organized businesses with transparent processes and the ability to make quick, data-based decisions. So let’s dive deeper into the technicalities.
Main asset tracking technologies: benefits and tradeoffs
As we said, there are many ways to track your assets that are based on different technologies. Let’s look at the main ones.
Main asset tracking technologies compared
Barcode tags: cheap solution for item-level tracking
Main usage: retail, warehousing, manufacturing
Barcode tags are the most popular, simplest, and cheapest asset tracking solution invented back in the 1970s. Unique tags can be attached to diverse asset types (containers, equipment, separate items) and then scanned with a reader or a smartphone. However, their main downside is that to be scanned, they have to be visible, i.e., be in a straight line of sight with a reading device. Also, the tags don’t contain any real-time status information. So basically they help with asset/inventory identification but not location tracking.
Barcode tags are mostly used in retail, warehousing, and manufacturing for inventory counts. In these cases, knowing the real-time location or exact asset condition is rarely necessary so barcodes are a decent, cost-effective solution.
QR codes: upgraded barcodes containing more data
Main usage: eCommerce, retail
QR codes are successors to barcode tags since they work on the same principle of attaching printed labels to assets that can be scanned, often with a smartphone. However, unlike barcodes, they can be read from any angle and contain way more information, i.e., product description, delivery date, customer details, destination, and so on.
This simplicity and low cost made QR codes greatly popular in eCommerce and retail businesses.
RFID tags: multipurpose technology with a plethora of applications
Main usage: retail, rail fleet tracking, warehousing, transportation
RFID or radio-frequency identification is another technology widely used in such logistics processes as transportation and inventory management. RFID tags are often attached to packaging or separate merchandise items to be scanned by handheld or stationary readers. Their big advantage over barcodes is that they don’t have to be visible when scanned.
Tags can either carry a unique unit ID number or have additional product-related information such as manufacturing date or batch number (up to several pages of data in total).
RFID tags can be read in bulk when passing by a scanner, which makes it a seemingly great solution for tracking multiple packaged or containerized items. However, such bulk readings are often unreliable as not all labels might be read (even though it works well when tracking a known group of items). Besides, the big weakness of RFID technology is its high sensitivity to interference caused by any RF transmitters in the area of reach.
There are two main types of RFID tags.
Passive RFID tags don’t have a battery and are activated with a radio frequency signal from a reader. They are cheaper and smaller, but they only transmit signals when actually scanned (manually or when passing through a scanning device-equipped zone), so no real-time information is available. That’s why they are often installed in so-called choke points in terminals or yards but aren’t effective when continuous asset tracking throughout a big territory is required.
Active RFID tags have an inbuilt battery and, working in combination with Bluetooth or GPS technologies, continuously transmit data. They don’t have to be scanned to get information, but because of such constant work, their battery life is limited. They have a longer read range (up to 300 feet or 100 meters), so they don’t need to pass through a fixed checkpoint to transmit data.
Active RFID tags are often sensor-enabled so they can collect and transmit additional asset information.
Within supply chains, RFID labels are popular in retail (that’s exactly the technology behind anti-theft security systems), rail fleet tracking, container/pallet-level tracking of shipments in warehouses/distribution centers (while separate items inside the packaging still often have barcodes), etc.
Bluetooth tags: compatible with multiple devices and long-lasting
Main usage: manufacturing
Bluetooth Low Energy (BLE) tags or beacons are especially effective for indoor asset tracking. As they consume small amounts of energy and last for years without the need for replacement, they became one of the most widely used components for IoT asset tracking systems.
BLE beacons are highly compatible with diverse Bluetooth-enabled devices such as tablets, smartphones, or computers, so there’s often no need to buy specialized readers.
Just like RFID tags, BLE beacons can be sensor-enabled. Their transmission range is comparable to that of active RFID tags, but their low cost, small size, compatibility, and long battery life make them a popular option for asset tracking in manufacturing facilities.
UWB tags: most accurate and least prone to RF interference
Main usage: manufacturing
UWB or ultra-wideband is another short-range radio technology that enables indoor asset tracking. UWB tags are battery-enabled, energy-efficient, have a range of up to 300 feet (100 meters), and have a high rate of data transmission.
Because of its precision, UWB technology is often implemented for item-level tracking. Given the clear line of sight with tracked objects, UWB provides submeter (up to 10-30 cm) location accuracy, unquestionably outperforming other solutions. They are also resistant to RF interference which makes UWB-based tracking systems fit for industrial environments.
Wi-Fi systems: use existing infrastructure but lack accuracy
Main usage: indoor tracking of existing Wi-Fi devices
Wi-Fi-based asset tracking systems make use of existing networks to transmit real-time location. That’s why their implementation is usually inexpensive. Another advantage of Wi-Fi systems is the possibility of quickly transferring big amounts of data.
However, Wi-Fi devices only provide basic location information, so to transmit more data, other technologies (e.g., BLE or UWB) have to be implemented. Other disadvantages of Wi-Fi-based tracking are low precision (around 15 meters or 50 feet), high energy consumption, sensitivity to signal interference, and security issues.
GPS devices: global outdoor tracking technology
Main usage: transportation (vehicle and container tracking while en route)
GPS-based tracking devices can transmit real-time location and status data via cellular networks or satellites over long distances. Telematics technologies that help track fleet movements, whether trucks, trailers, or railcars are typically GPS-based.
In addition to just tracking location, telematics data comes in handy for a variety of fleet management operations like maintenance, routing, driver behavior assessment, fuel management, and so on.
Besides, GPS devices are widely exploited in cold-chain logistics. Attached to shipping containers, they help monitor temperature, humidity, and other important conditions.
LoRa systems: energy-efficient long-distance tracking
Main usage: tracking within large facilities with both indoor and outdoor areas
LoRa or long-range technology enables asset tracking over large distances. But unlike GPS, it uses less power which makes it more efficient and extends battery life for years of operation. LoRaWAN, the communication protocol based on the LoRa technology, is frequently used in IoT infrastructures due to long-range transmission capabilities (up to 30 km or 18.5 miles) and low power consumption.
However, since it’s the newest technology of all we mentioned earlier, its implementation is comparatively more expensive. It also lacks precision.
There are also other data-transmitting technologies like NFC that are rarely used for asset tracking purposes due to their limitations.
Which asset tracking technology to choose?
Technology choice depends on your needs and resources. Price is often the key limiting factor (and the range is huge, e.g., BLE tags are 100 times more expensive than RFID tags, and the UWB type cost even more) so you must conduct a thorough cost-benefit analysis and calculate which implementation project is worth the ROI. But there are also other important aspects to decide on.
Which assets and how many of them have to be tracked? For example, if you need to locate thousands of SKUs in your storage space, you most probably need a cost-effective solution like barcodes. But if you want to monitor equipment usage or movements, this tracking technology won’t work as you need greater data accuracy.
Do you need to track location only or collect other asset-related information? For example, if you deal with perishable/fragile items, you need sensor-enabled tags that collect data on such essential parameters as temperature, humidity, vibration, etc.
How accurate should location tracking results be? As we said, UWB is the champion in precision so it’s a good option for tracking tools, devices, or other small items but be ready to install multiple readers all over the place to achieve this accuracy. However, if you track vehicles, massive equipment, or machinery, room-level accuracy is enough.
Do you need indoor, local, or global tracking? GPS is a perfect global tracking technology but if you have to track vehicles and outdoor equipment, make sure the hardware can withstand harsh weather conditions and extreme temperatures. As for indoor environments, take into account other radio transmitters that can interfere with your tracking devices (especially BLE or Wi-Fi based). If that’s the case, UWB technology is most resistant to surrounding narrowband technologies.
Do you need real-time tracking? Again, as we said, if getting tracking information intermittently is enough for you (say, if you run a terminal or distribution center), you can go with a passive RFID-based system and install readers in gateways and other choke points to track assets as they pass by. However, if you need to continuously monitor equipment movement, you’ll have to develop a complex IoT system.
Often, there’s no perfect answer to which technology is the best as all of them have their strengths and weaknesses. That’s why, in many cases, tracking systems combine several technologies for the utmost results.
Asset tracking software and use cases
As you can already see, there’s a wide range of requirements for asset tracking that create a similarly wide range of solutions. You can’t just Google “what’s the best asset tracking software out there” and get a one-size-fits-all recommendation because the technologies are completely different, say, for tracking tools in the manufacturing environment vs monitoring cargo hauled across the country.
So let’s try to roughly categorize the most common scenarios.
Tracking vehicles or shipping containers
If you need to track your fleet (trucks, trailers, railcars, etc.), a GPS-based telematics system is the most suitable solution. As we described above, such software not only provides real-time location data but also supports other fleet management processes such as fuel management, maintenance, and so on. GPS devices attached to containerized shipments work correspondingly.
Some recognized providers of GPS tracking products are Verizon Connect, Samsara, Azuga, and Teletrac Navman.
Tracking inventory in retail
In retail, you don’t need to know the real-time location of each and every item you sell. Instead, you need to monitor the constant inbound and outbound flow of multiple SKUs as part of your overall inventory management routine. Barcodes and QR codes are a common standard adopted by most manufacturing companies so you can just make do with them to streamline your inventory counts and stock management.
RFID tags are often attached either to pallets for batch tracking or to separate high-value items to prevent theft so that’s another popular technology used in retail.
As for software, you can get all the necessary features in your retail management or inventory management system. Some of the popular products in this category are Katana (both barcodes and RFID supported), Zoho Inventory (barcodes), Sortly (barcodes and QR codes), Cybra’s MarkMagic/Edgefinity IoT (barcodes/RFID), and so on.
Tracking tools, small equipment, and spare parts
Spending half a shift looking for a misplaced hammer or grinder is definitely not a good use of time. Manufacturing plants and construction sites often have a significant stock of tools, small equipment, or parts that are used by different workers and are hard to track.
Tool tracking software typically allows users to
- quickly look up the item location and usage history;
- check tools in and out with a smartphone;
- assign equipment to teams, projects, or workers;
- store warranty information and user manuals, etc.
Some solutions even have additional handy functionality like maintenance alerts.
Most tool tracking systems offer basic barcode/QR code tracking with intuitive mobile scanning functionality (e.g., ShareMyToolbox or GigaTrac).
GigaTrac interfaces
Other products offer more advanced capabilities. For example, ItemAware scans RFID tags (which allows you to get real-time updates whenever items leave or enter designated zones), GoCodes shows the current location due to GPS technology (which is a great option if you often move tools between sites), and ToolWatch supports BLE and RFID tracking.
Tracking movable equipment and machinery
Tracking forklifts, AGVs, and other handling equipment is crucial not only for the mere sake of knowing where they are at any given time but also to find optimization opportunities (e.g., adjust routes or detect underutilized equipment).
Today, UWB-based RTLSs are gaining traction in warehousing and industrial environments as they provide the most accurate real-time positioning. They are also least prone to RF interference and are very energy efficient. UWB tags can be equipped with sensors to monitor other measurements besides location (such as shock or vibration). Sometimes, UWB is coupled with BLE or RFID technology as well.
We’ll briefly explain how such systems function.
First, UWB tags have to be attached to the equipment, and readers or anchors have to be installed on ceilings or walls throughout the facility. Tags continuously transmit signals that are captured by anchors. Collected data is then transferred to the server, either local or cloud-based. To make implementation easier, existing Wi-Fi networks are often used. The servers interpret the received information and pass it on to business applications where users can view it and interact with it (e.g., make reports, conduct analytics, etc.).
These systems also allow for geofencing and setting up multiple business rules for automating various processes. For example, you can configure the system to automatically stop the vehicle when someone is in close proximity to avoid accidents, set up alerts if equipment leaves the designated zone, or restrict access to certain areas.
Most providers of RTLSs offer turnkey services which include hardware, software, installation, system customization, training, etc. Some RTLS vendors are Sewio, WISER, Litum, Ubisense, and so on.
Importance of asset tracking system integration
There’s one more crucial aspect we have to discuss, namely, the integration of an asset tracking system. Integration in general is essential to establish seamless data exchange between various components or modules of your IT ecosystem. So if you already have a business management application (WMS, WES, IMS, ERP, etc.) that you want to enhance with asset tracking software, you have to consider building a connection between them.
Once you have such an integration in place, you can easily share diverse information between your systems, e.g., transfer SKU details to monitor inventory levels, know your container location to calculate ETA, or view equipment route patterns to analyze efficiency in the business intelligence tool.
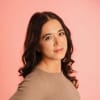
Maria is a curious researcher, passionate about discovering how technologies change the world. She started her career in logistics but has dedicated the last five years to exploring travel tech, large travel businesses, and product management best practices.
Want to write an article for our blog? Read our requirements and guidelines to become a contributor.