Digital twins play the same role for complex machines and processes as food tasters for monarchs or stunt doubles for movie stars: They prevent harm that otherwise could be done to precious assets. Having made their way to the virtual world, duplicates save time, money, and effort for numerous businesses, protecting the health and safety of high-value resources.
The article covers key questions about digital twins: How do they work? What are they capable of? Who already uses them, and for what reason? And—most importantly—what does it take to adopt them?
What is a digital twin?
A digital twin (DT) is a detailed and dynamically updated virtual replica of physical objects or processes made to monitor performance, test different scenarios, predict issues, and find optimization opportunities. Unlike traditional computer-aided design and engineering (CAD/CAE) models, a DT always has a unique, real-world counterpart, receives live data from it, and changes accordingly to mimic the origin through its lifecycle.
Imagine an aircraft engine with sensors that track temperature, pressure, and vibration in real time. This engine's digital twin, or virtual model, mirrors these conditions. Engineers can use the twin to simulate wear and tear, schedule maintenance, and predict possible failures.
Digital twin modeling: a bridge between the physical and virtual worlds
The digital twinning process includes iterative operations to provide a data flow between physical and digital domains. The sequence of these operations, or DT lifecycle, is called a digital thread.
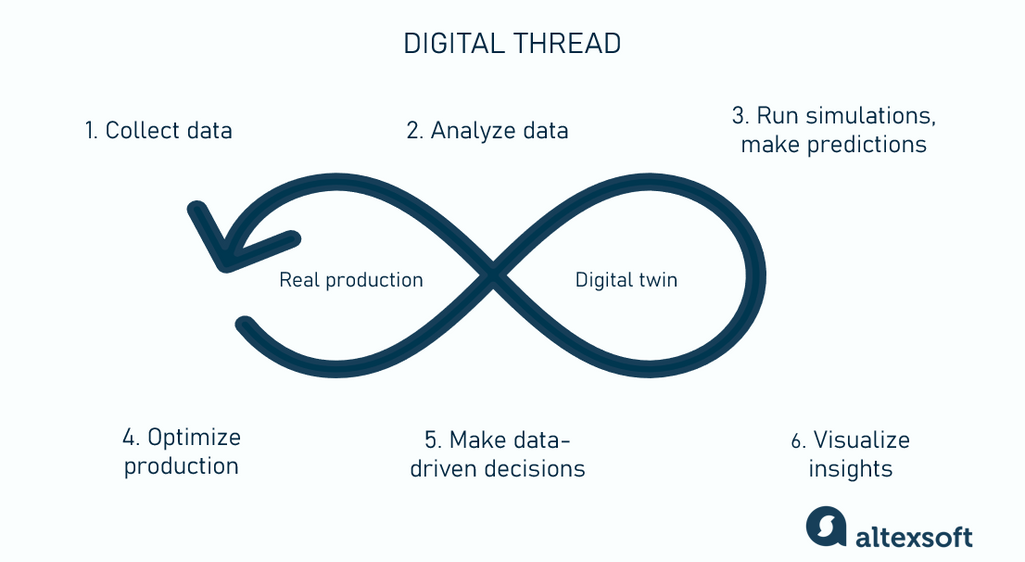
Steps within a digital thread.
- Data is collected from a physical object and its environment and sent to the centralized repository.
- Data is analyzed and prepared to be fed to the DT.
- The digital twin uses fresh data to mirror the object’s work in real time, test what will happen if the environment changes, and find bottlenecks. At this step, AI algorithms can be applied to tweak the product design or spot unhealthy trends and prevent costly downtimes.
- Insights from analytics are visualized and presented via the dashboard.
- Stakeholders make actionable, data-driven decisions.
- The physical object parameters, processes, or maintenance schedules are adjusted accordingly.
The process is then repeated based on the new data. Digital twins reduce the complexity of the real world to the information necessary for decision-making, which is why the technology is welcome across many industries.
Here’s an illustrative example of how a digital twin system works. Imagine that a temperature sensor’s data on a wind turbine shows increased bearing temperature during operation. The analysis demonstrates that this rise coincides with high wind speeds. To find safe limits, the digital twin simulates operating the turbine under varying wind speeds. It predicts at what wind speeds the bearings could be damaged. The dashboard shows a warning about the temperature trend. The company owning the turbine decides to adjust its operating settings to reduce its rotation speed when wind speeds exceed a safe limit.
Digital twin use cases and types
First introduced in 2002 by Dr. Michael Grieves as a new approach to managing product life cycle, the concept of digital twins gained traction in many areas, including supply chain management, remote equipment diagnostics, predictive maintenance, and more. They can serve any phase of product development, from design to post-production monitoring and servicing.
Of course, virtual modeling doesn’t work as well for every business. Its implementation comes with a hefty price tag and may make little to no economic sense for simple products. Virtual models suit complex and large-scale projects and multi-component mechanisms, finding the most successful applications in
- construction of buildings, bridges, drilling platforms, and other large objects;
- industrial environments;
- designing and manufacturing complex products like cars, jet turbines, airplanes, or new drugs;
- city planning; and
- the energy sector with its massive equipment for power generation and transmission.
Within these industries, twinning can be done at different levels — from a separate component to the entire product to production to a system of systems.
Component twinning
The basic level of twinning allows engineers to evaluate the durability, resilience, energy efficiency, and other characteristics of a product's separate parts. They can use simulation software to analyze how the component in question will behave under static or thermal stress and in other real-life scenarios.
Product or asset twinning
The replica of the entire product reveals how individual components work together under various conditions and what can be done to achieve better performance and reliability. Digital twinning can also be used to design new technical solutions instead of creating multiple prototypes. This shortens development time and allows for faster iterations.
Process and production twinning
Digital twinning is applicable not only to physical assets but to processes as well. In this case, you create complete virtual models of the production steps.
This approach helps answer important questions like: How long will it take to produce a particular product? How much will it cost? Which machine should do what? Which steps can be automated? Is the production of a particular item feasible at all? Additionally, visualizing the entire production process makes it easier to prevent costly downtimes.
System twinning
A digital twin of the system brings visibility to complex interconnections and interdependencies of products and processes. The twinned system can replicate something as large as a multistory building, electrical grid, or even a whole city, which can be viewed as “a system of systems.” However, investment to build such a replica, in many cases, may not equal the hoped-for return. That’s why system twinning is not as widespread as other DT types.
Digital twin system: hardware and software
A digital twin system contains hardware and software components with middleware for data management in between.
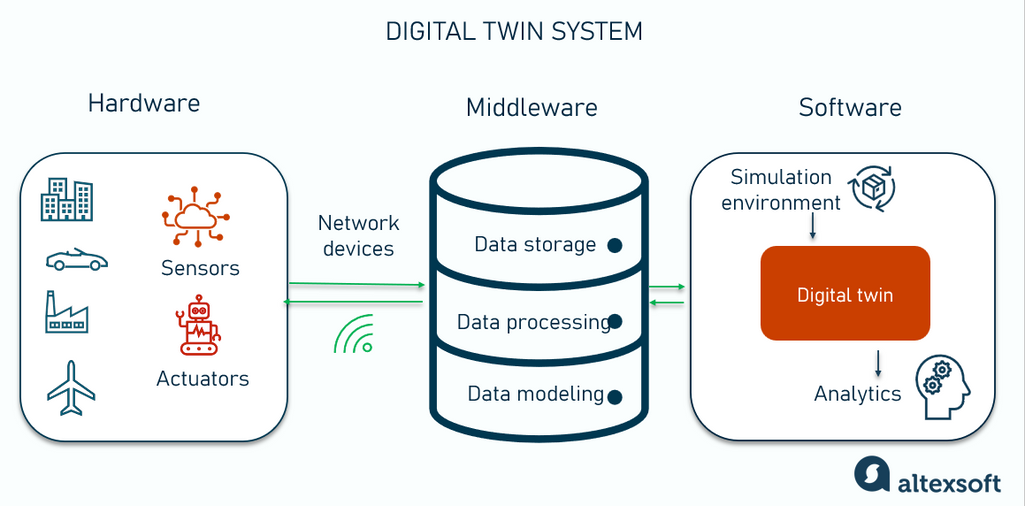
Components of the digital twin system.
Hardware components. The key technology driving DTs is the Internet of Things (IoT) sensors, which initiate the exchange of information between assets and their software representation. The hardware part also includes actuators, converting digital signals into mechanical movements, network devices like routers, edge servers, and IoT gateways, etc.
Data management middleware. Its bare-bones element is a centralized repository to accumulate data from different sources. Ideally, the middleware platform also takes care of such tasks as connectivity, data integration, data processing, data quality control, data governance, and more. Examples of such solutions are common IoT platforms and industrial (IIoT) platforms that often come with built-in tools for digital twinning.
Software components. The crucial part of digital twinning is the analytics engine that turns raw observations into valuable business insights. In many cases, it is powered by machine learning models. Other must-have pieces of a DT puzzle are dashboards for real-time monitoring, design tools for modeling, and simulation software.
Digital twin simulation
A simulation is a one-time or iterative computational experiment that mimics the behavior of a system under specific conditions. It’s used to test scenarios, designs, or hypotheses, identify weaknesses, and make more informed decisions. For example, testing how a car might behave in a crash at different speeds is a simulation.
Broadly speaking, simulation relies on mathematical modeling and predefined datasets; it does not necessarily involve real-time data updates. It is often part of new product development during the model-building phase. However, in the context of digital twins, data for simulation is obtained from real objects. This way, simulations become more accurate because they are based on the behavior of an existing product or process.
While the digital twin offers a comprehensive representation of the system, simulations bring it to life, unlocking its full potential for analysis and optimization.
Digital twin examples
Below, we’ll give real-life examples of how digital twins work in different industries across all levels.
Digital twin in the aircraft industry: pinpointing the right time for engine maintenance
Up to 70 percent of airplanes in the world fly on engines produced by General Electric (GE). This fact makes the corporation partially responsible for the safety of millions of passengers. To forecast the degradation of the aircraft’s heart over time, GE created a digital twin for its engine, GE90, that powers the long-range Boeing 777.
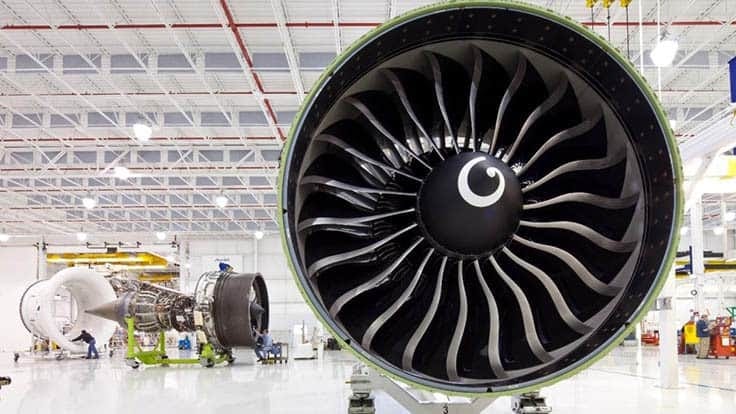
The twin represents not the entire mechanism but its composite fan blades, which are prone to spallation or the peeling off of material fragments due to the impact of rough conditions. This is especially true for regions like the Middle East, where engines are exposed to an additional damaging factor: sand. The DT helps pinpoint the right time for maintenance before any issues arise.
Digital twin in hospitality: enhancing guest experience
Radisson Hotel Group, Hyatt, and other chains collaborate with the Hotelverse platform to create virtual replicas of hotel properties, allowing travelers to explore rooms online before booking. Guests can see window views, room layouts, or sunlight exposure to make more informed choices, leading to a 30 percent increase in superior room bookings. The digital twin integrates with the hotel property management systems (PMSs) and shows available rooms in real time.
Digital twin in the automotive industry: running car replicas for remote diagnostics and improving race results
Each new car produced by Tesla has its own digital twin. Sensors embedded in a vehicle constantly stream data about the environment and performance to the virtual copy that lives in the cloud. AI algorithms analyze these feeds to identify whether the car works as expected. If not, the problems are fixed by sending over-the-air software updates.
In this way, Tesla adapts the vehicle’s configurations to different climate conditions, virtually improves its performance, and provides remote diagnostics, minimizing the need for visiting service centers.
You can read about other approaches to vehicle maintenance in a dedicated article.
McLaren, a British luxury automotive manufacturer, uses digital twins to improve the results of McLaren’s F1 team. Each car has 300 sensors, monitoring factors like airflow, temperature, and speed and collecting about 0.7 terabytes of data per race. Machine learning algorithms process this data to detect patterns and inform critical decisions, such as tire changes or pit stops. Digital twins based on real-time data enable McLaren to run up to 200 simulations during a race weekend, exploring scenarios like rain or safety car deployments. This data-driven approach enhances strategy, efficiency, and adaptability in the highly competitive world of Formula 1 racing.
Digital twin in manufacturing: reducing the wear of wheels
Bridgestone, the world’s top tire and rubber manufacturer, regularly uses digital twins to understand how speed, road conditions, driving style, and other factors affect the performance and lifespan of its products. Armed with these insights, the company helps fleets select the best options for their specific needs and advises on what can be done to prevent damage and extend the life of the wheels.
The industry leader also uses digital twinning to design and test new types of tires. According to Bridgestone estimations, this approach cuts development time by 50 percent.
Digital twin in power generation: predicting the performance of gas turbines
Siemens, Europe's largest industrial manufacturing company and a digital twinning pioneer, developed a virtual avatar of its gas turbine and compressor business purchased from Rolls-Royce. The digital twin called ATOM (Agent-Based Turbine Operations and Maintenance) represents the production and servicing of their turbine fleet, spanning the supply chain operations.
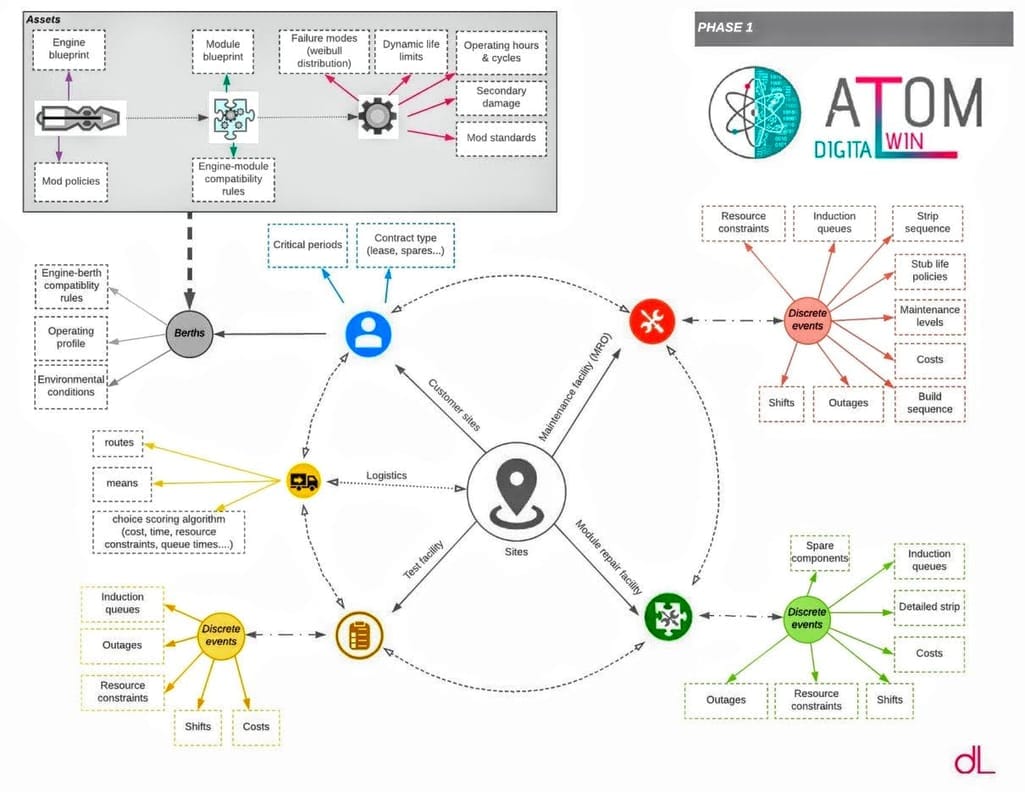
ATOM digests live data from multiple sources to thoroughly model cobwebs of engine parameters, performance metrics, maintenance operations, and logistics steps throughout the entire turbine lifecycle. Running different what-if scenarios and visualizing their results helps stakeholders make better investment decisions.
Digital twin in supply chain: bringing visibility to logistics
In September 2021, Google presented a new service that enables companies to build digital twins of their physical supply chains. The solution focuses on organizations in the retail sector, healthcare, manufacturing, and automotive industries. It aggregates information from multiple sources into one place and helps customers get a complete and clear view of their logistics.
Google claims that the DT paves the way to much faster data analysis: Tasks that previously took up to two hours now take just a few minutes. With its fresh offering, the company is snapping at the heels of IBM, Amazon, and Microsoft, all of which launched supply chain and other digital twin options a little earlier.
Digital twin in construction: creating profiles of buildings to reduce energy consumption
Automatic Building Energy Modeling, or AutoBEM for short, enables the generating of digital twins for any building in the US. The project took the developers from the Department of Energy’s Oak Ridge National Laboratory five years and became available in 2021.
AutoBEM relies on public information like satellite imagery, street views, light detection and ranging (LIDAR), prototype buildings, and standard building codes to generate energy profiles of structures. A twin reflects all critical external and internal characteristics, including height, size, type, number of windows and floors, building envelope materials, roof type, heating, ventilation, and cooling systems.
Advanced algorithms behind the twin predict which technologies will be implemented to save energy. These include modern water heaters, smart thermostats, solar panels, and more. AutoBEM is supposed to be widely used in urban planning and maintenance, as there is much concern about energy consumption in cities across the US.
Digital twin in healthcare: an alternative to human and animal trials
A French multinational software corporation, Dassault Systèmes, in collaboration with the FDA, created SIMULIA Living Heart, a digital twin of the human heart. Such a model can help speed up clinical trials for heart disease drugs and cardiac device innovations. For example, In 2024, SIMULIA Living Heart was used for simulating transcatheter aortic valve replacement (TAVR) to study stent fatigue in a beating heart, which helped enhance device design to make stents more durable. This approach offers a cost-effective alternative to human and animal trials.
The Cleveland Clinic employs digital twins of local communities to study and address healthcare disparities linked to geographic and socioeconomic factors. By analyzing anonymized electronic health records, these models incorporate biological, social, and environmental data to simulate neighborhood health dynamics. This way, researchers can evaluate various health initiatives and new services, as well as understand how relocations affect people’s health.
Digital twin implementation
Theoretically, you can build a digital twin for almost everything. In practice, creating a replica that covers every single aspect of a product or manufacturing process is far from feasible. If you’ve already concluded that your business will benefit from DTs or at least, want to test the idea, choose your business's most vulnerable or crucial single component or operation.
Once you understand what you are going to twin in the first place, the next steps may be the following.
Choose the type of digital twin: physics-based vs data-driven vs hybrid models
Generally, there are two types of DTs—physics-based twins and data-based twins. The former rely on physical laws and expert knowledge. They can be built from CAD files and used to simulate the work of comparatively simple objects with predictable behavior—like a piece of machinery on the production line.
The key downside is that updating such twins takes hours rather than minutes or seconds. So, the approach makes sense in areas where you don’t need to make immediate decisions.
Contrasted with the physics-based type, data-based twins rely on deep learning models to find hidden patterns.
They offer more accurate and quicker results and are applicable to products or processes with complex interactions and a large number of impact factors involved. On the other hand, the approach needs a vast amount of information not limited to live streams from sensors to produce valid results.
Models must be trained on historical data generated by the asset itself, accumulated from enterprise systems like ERP, and extracted from CAD drawings, bills of material, Excel files, and other documents.
Today, various combinations of two methods—or so-called hybrid twins—are often used to achieve the best of both worlds.
Narrow down the focus
Even if we’re speaking of the same component or product, different models are to be created for different tasks. For example, the General Electric Digital department defines four categories of models that can be integrated into the DT designed for the needs of power plants.
Living models track equipment conditions and forecast how it will age, providing for its operations and exposure to damaging factors. This helps optimize maintenance outages and extends the asset’s working lifespan.
Anomaly models are responsible for early fault detection to reduce unplanned downtimes.
Thermal models simulate parameters related to thermal efficiency to better manage degradations.
Transient models predict the plant’s speed, reliability, and emissions under different conditions. The insights gained are used to achieve the best operational flexibility, taking into consideration equipment and site limitations.
Anyway, at this step, you need to define what exactly your model will do: monitor conditions, prevent faults, simulate behavior under different parameters, help in product design, you name it. Focus on one task, test results, and only then augment your digital twin with other capabilities.
Consider investments to be made
Suppose your company already has sensors and CAD or CAE software to create a basic representation of your assets. In the next phase, you will have to invest in
- additional hardware—for example, edge computing devices to process data on the periphery, closer to IoT sensors;
- services of a data management or IoT platform or other middleware to ingest and process data from disparate systems and store it in one place;
- simulation software;
- analytics solutions;
- domain experts; and
- data engineers, data scientists, and other data experts..
It’s worth noting that large cloud providers and leaders in digital twinning offer services that cover many aspects of digital twinning.
Explore ready-to-use data twin solutions
Here’s a short overview of the DT products from industry leaders that will save you time and effort.
Azure Digital Twins is a platform as a service (PaaS) for visualizing physical environments with all connected devices, locations, and occupants involved. The relationships between these objects are represented with spatial graphs. The service is paired with Azure IoT Hub, which collects data from IoT sensors and other Azure services.
HxGN SDx2 is Hexagon's cloud-native SaaS platform that enables advanced visualization of 2D and 3D models, geospatial data, point clouds, and panoramics (Hexagon claims to have the world’s largest database of geospatial content). It integrates data from various sources, including Hexagon and third-party tools. Role-based dashboards provide user-specific views that integrate datasets across workflows.
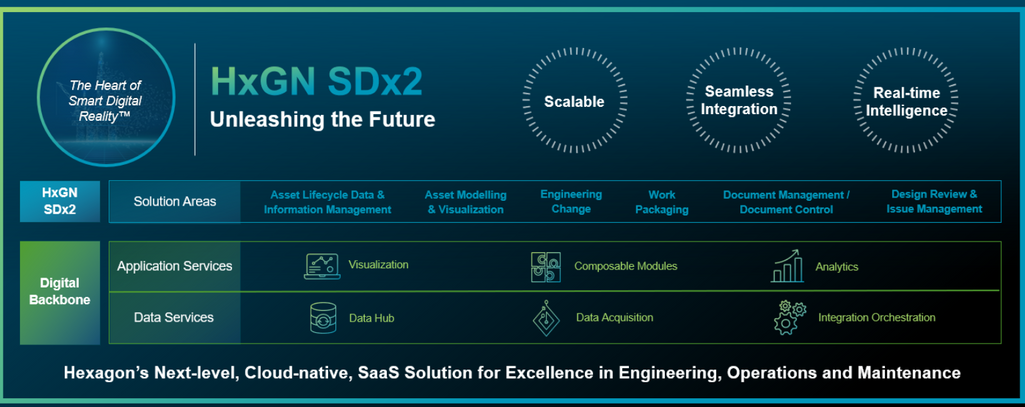
HxGN SDx2 features. Source: Hexagon
GE Vernova Digital Twin Technology allows companies to rapidly create digital twins and get value from them, using "blueprints" from their catalog. The three core areas covered by GE are manufacturing assets, grid networks, and production processes. DT software is powered by machine learning.
Oracle IoT Digital Twin Framework enables you to create both physics-based and data-driven or predictive digital twins. The former compares observed and desired parameters to detect existing problems. The latter run machine learning algorithms to forecast future issues and prevent or prepare for them.
Keep in mind, though, that DT tools, elements, and blueprints work well when bought from one vendor. Otherwise, compatibility and integration issues are more than possible. As with other emerging and evolving technologies, digital twinning lacks generally accepted standards, leading to poor system interoperability.
Remember, there’s no off-the-shelf digital twin technology
In any case, each DT is as unique as the product or process it represents. Ready-to-use infrastructures, platforms, and models can facilitate development but won’t do all the work. You will still need experts in data, machine learning, cloud technologies, and, of course, engineers capable of integrating different parts of hardware and software puzzles.
What to expect?
Digital twins enable companies to create new products in a virtual environment, minimizing risks and reducing costs. This is why leading global corporations are investing heavily in DTs. Approximately 75 percent of advanced companies, primarily in the automotive, aerospace, and defense industries, have already implemented this technology. More and more tech leaders, including Microsoft, GE Digital, and Dell, have joined the Digital Twin Consortium to facilitate DTs' development, adoption, and interoperability.
In the digital transformation era, digital twins help transition to a more sustainable and agile economy, offering companies advantages in highly competitive markets.