Managing freight involves numerous processes -- and always leaves room for optimization, cutting expenses, and streamlining daily operations. Today, implementing modern technologies can increase supply chain efficiency, whether it concerns routing, tracking, warehousing, or other industry-specific issues.
In this article, we’d like to talk about the load planning process and related challenges -- and describe how software can help solve the “empty space problem” in logistics.
What is load planning?
Load planning, also called load optimization, is the process of consolidating multiple shipments and/or arranging freight to use the capacity of trucks, railcars, pallets, and any other types of containers in the most efficient way. The main goal is to reduce transportation costs by using fewer vehicles or containers to move freight. In addition to that, optimizing shipments helps avoid damaging cargo, save loading and unloading time, and ultimately, increase customer satisfaction.
Moving freight is a very complicated process with multiple options for interactions between parties. The length of the supply chain can range from a simple manufacturer-carrier relationship to a multimodal, multi-leg journey, involving a number of intermediaries (i.e., manufacturer to wholesaler to retailer to freight forwarder) and reloading in several ports/terminals/distribution centers.
Creating an optimal cargo configuration is essential for different players in the logistics industry -- basically, anyone who deals with loading multiple items.
Depending on the container/truck filling, two main scenarios exist.
FCL/FTL shipment
Dealing with full container loads (FCL) or full truckloads (FTL) is usually cheaper than partial loads (comparing price per unit or cubic meter) and easier as it involves fewer intermediaries. In case of FCL/FTL shipments, shippers (manufacturers and retailers) fill the shipping containers or trailers themselves and hand them over to the carrier to deliver to the destination.
The challenge appears if such a shipment consists of multiple items. Those shippers and carriers that move varied freight and/or handle different types of packaging have to find an optimal way to stack their cargo in the equipment. Let’s look at a hypothetical example of such a shipment.
FCL/FTL shipment flow
Imagine you own an internet store of technical devices and equipment in Chicago and order supplies from China. Your order is big enough to fill up the standard 20’ shipping container. So, your supplier in China uses a load planner to pack all the items you need so that they all fit in the container, stability and stackability constraints considered.
Then, this container is handed over to the shipping company that uses a load planner to configure the optimal loading of multiple containers on the vessel, considering balance constraints, weight, dimensions, etc.
If not distributed correctly, containers can collapse, source: wvxu
Once the shipment arrives at, say, Newark or Baltimore port, it’s reloaded and put on a railcar to be delivered to Chicago. There, you finally receive your ordered inventory and allocate it to your warehouse. The next day a big order comes in from one of your Cincinnati clients. So, you find a carrier with a dry van and use the load planner to stuff the boxes with ordered items in the trailer, again, keeping in mind the balance, fragility, stackability, and other possible constraints.
LCL/LTL (consolidated) shipments
Less-than-truckload (LTL) and less-than-containerload (LCL) shipments in most cases involve consolidation to reduce transportation costs. That means that carriers, 3PL, and freight forwarding companies that work with multiple shippers have to combine freight and arrange it in a truck or container considering a number of restrictions.
LCL shipment flow
For example, you order 25 boxes of sundry metal spare parts in China for your auto repair shop. Your supplier would most likely palletize the boxes (load planning can be used for palletization as well) and get those pallets to a freight forwarder that specializes in consolidation. The weight, dimensions, type of package, safety measures, and handling requirements of cargo would be listed in the bill of lading, air waybill, and export packing list.
The consolidator collects such LCL shipments from different shippers and with the help of a load planner assembles them into FCLs. When the shipment gets to a port of destination, it is deconsolidated and sent by rail or truck to the receiver.
When you get your parts, somebody orders 15 boxes from you. So, if you use a trucking company to move them, it will be an LTL shipment and will be combined by the carrier with other cargo. The carrier would collect the BOLs listing weights and dimensions of all LTL shipments and plan a load to arrange them in a trailer in such a way that space usage is maximized and all balance and safety constraints are met.
Balance is important, source: Mex Files
Traditionally, a person holding the position of load planner would manually build loads and draw diagrams, taking into account all the possible constraints and requirements. Obviously, it’s too complicated, time-consuming, and error-prone if done by hand.
So, using specialized software can improve the efficiency of the load planning process, save time, and increase the accuracy of your load calculations. Let’s see what such software can do.
Load planning software features
Different software providers offer different functionality. If you’re choosing an off-the-shelf product, customizing the one you already have, or considering creating your own solution, here are some useful features that you might need to cover your requirements.
3D diagram creation
Generating visual, easy-to-understand load plans is one of the primary functions of load planning platforms. 3D diagrams are a lot more demonstrative and convenient to work with than 2D. See yourself.
2D vs 3D load plans
Interactive 3D graphics make it possible to rotate the load plan, zoom in and out, and easily locate the items.
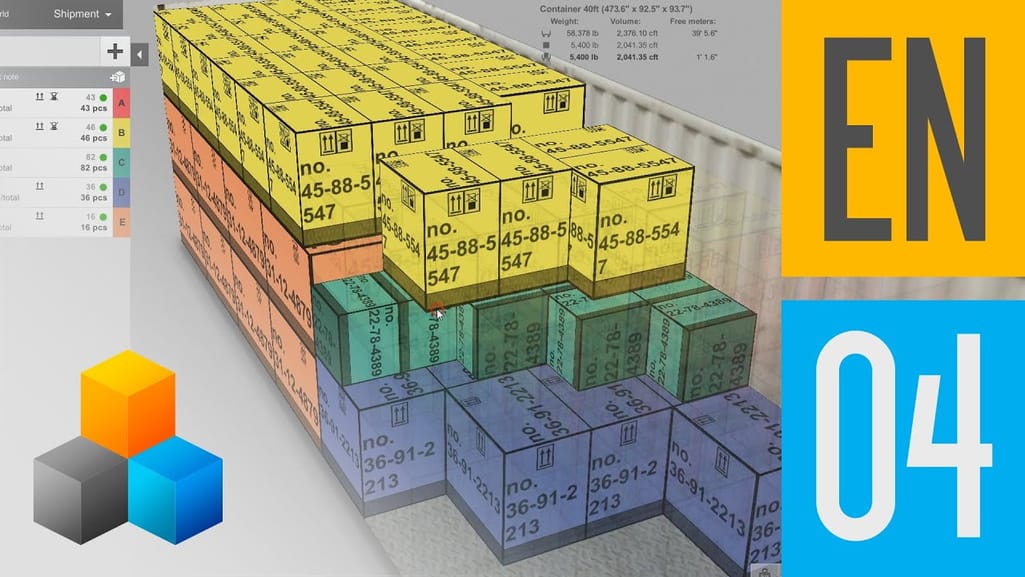
3D load plan visualization control (EasyCargo)
Different types of trailers/containers
The load planning software has to be able to solve such business tasks as packing items into boxes, palletizing boxes, and trailer/container-loading. Also, there should be options for side, top, and front-loading.
A good tool has to include a database of container and trailer types and offer the ability to easily switch between them. You might not use all types of containers to ship your goods, so when choosing or developing a load planner, focus on the ones that you need. For example, CubeMaster offers cheaper editions that only cover palletizing and don’t support trailer loading and vice versa.
Containers can be classified depending on the mode of transportation. Standard maritime containers include
- general purpose (dry) containers,
- flat rack containers,
- open top containers,
- high cube containers,
- reefer containers, etc.
All of them are typically 20 or 40 feet long (other dimensions are less common). There are also specialized containers, i.e., car carriers, tanks, drums, and so on.
Some popular container types
For railroad transportation, the general purpose and high cube containers are usually used.
Air freight containers are also called Unit Load Devices (ULD). They are developed and created from materials approved by the International Air Transport Association (IATA) and the Air Transport Association of America (ATA). ULDs also come in a wide range of shapes and sizes.
Air freight container types, source: Speedlink
In the trucking industry, a number of different trailers are used, depending on the product or commodity that is hauled. The most common ones are
- dry van,
- reefer,
- flatbed,
- step deck,
- double drop, etc.
Some popular trailer types, source: FARGO
For warehouses, load planning software has to offer a variety of packing options, such as pallets (industrial and Euro), totes, cartons, etc. Most load planners work with standard rectangular/cubic boxes and pallets, so if you often need to move freight that comes in other shapes or packages (cylindrical, L-shaped, etc.), make sure such options are supported.
Multiple constraints support
Load optimization is not only about stuffing as many boxes in a truck or container as possible. It deals with a multitude of various constraints and factors that have to be considered when planning a consolidated shipment.
Equipment constraints relate to total capacity and other physical characteristics of the container or equipment that is being loaded, such as side doors, bulkheads, number and size of compartments, inside temperature, etc.
Product constraints include any product-related properties, restrictions, or requirements, such as size, weight, shape, package type, stackability, fragility, required temperature, etc.
Compliance with regulations mainly concerns weight restrictions and handling hazmat freight to ensure overall transportation safety.
Customer requirements concern possible customer demands of handling their shipments. For example, all the items shouldn’t be placed in a single vehicle or container to reduce the risk of theft. Another common requirement is not transporting some groups of cargo together, i.e., food with chemicals.
Balanced distribution
It’s important that the load planning software configures loads in such a way that the weight is distributed considering the center of gravity of the trailer/railcar/vessel. In trucking, it’s also necessary to ensure that the trailer axles are not overloaded.
Axle load distribution, source: EasyCargo
Manual adjustments
There are situations when you have some unusual loading requirements or customer demands. In this case, it’s necessary to be able to adjust the load plan manually, select an optimal placement or position of cargo, improve stability, etc.
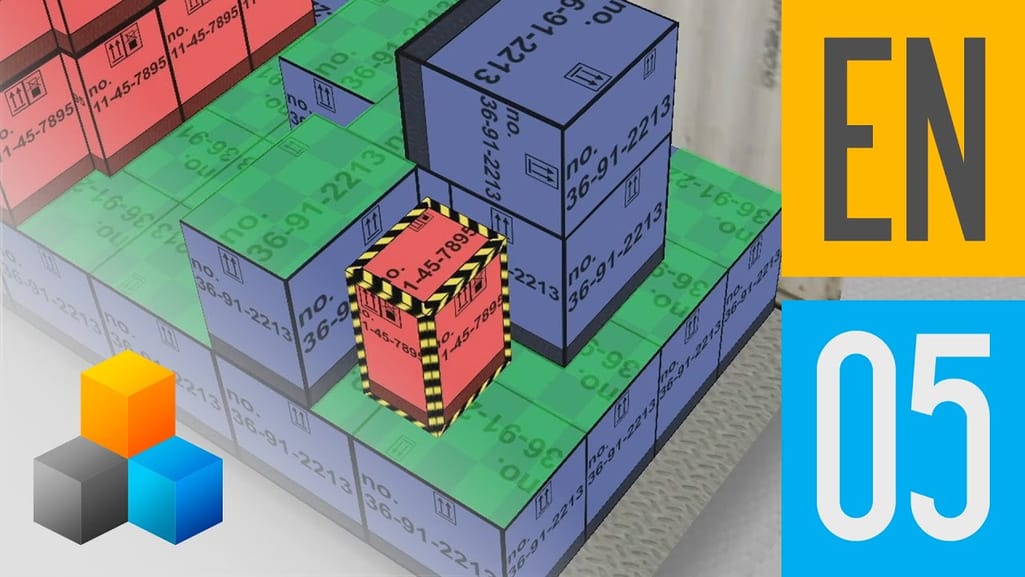
Manual load plan adjustments
Freight grouping, loading sequence, and step-by-step instructions
Frequently orders of different shippers or customers are moved together as a consolidated shipment. In this case, items that have to be shipped first (i.e., perishable products or ones having strict delivery deadlines) should be prioritized to be added to the load list in the first place.
Freight grouping (generated by EasyCargo)
Or items that have to be delivered to the same drop-off point should be grouped together and loaded considering the delivery sequence. The order of loading is important to ensure that the shipments are organized in the right order so that the loads to be delivered (or reloaded) first are easily accessible. Load planning software has to support freight grouping and sequencing.
Besides, being able to create detailed instructions can save loading personnel a lot of time. Instead of having your workers try to figure out the optimal stacking order themselves, it’s better to create and provide them with a printed step-by-step load plan, so be certain that such a feature is provided.
Step-by-step load plan by EasyCargo (see full version)
Integration options
Integrating different pieces of software in a single system streamlines operations and enables efficient and complete data sharing. Many TMSs offer load planning functionality as one of the modules. However, if you have or consider acquiring/creating a separate load optimization tool, it’s definitely worth connecting it to other software pieces via APIs, so it’s great to have available API information.
Load planner integration options
Integration with routing tools. As we mentioned earlier, the loading sequence is crucial for consolidated freight that involves multiple stops for either reloading (in a transitional port, warehouse, DC, etc.), pick up, or drop off. Since routing software creates the delivery routes and schedules, sharing this information with a load planner would enable building loads with an optimal loading sequence.
Integration with business management systems. Manually entering load lists takes too long and can result in errors. Most load planners allow for importing a load list with all the necessary dimensions from spreadsheets. However, it’s also helpful to establish a two-way integration with your business management system, such as
- enterprise resource planning (ERP),
- logistics management system (LMS),
- transportation management system (TMS), or
- warehouse management system (WMS).
With such connectivity, you could not only share the list of items to be loaded, but also available trucks and their characteristics, items grouping information, product dimensions and constraints, and much more. After the load plan is calculated, it will be sent to your TMS/ERP/WMS/LMS to update the inventory levels, truck availability, etc.
It’s also necessary to be able to save the load plan in various formats (xls, xml, HTML, PDF), share it via email, and print it out.
Integration with BI and analytics tools. Monitoring performance is vital for effective decision-making. Knowing how much freight you move, how loaded your containers are, how many packages fit in one truck, how load planning influences delivery time or accident frequency, etc., can help you obtain valuable insights and make further adjustments to optimize your supply chain performance.
Load planning software providers
In this section, we’ll briefly describe some popular providers that offer load optimization solutions. Most load planning tools are universal and can be used in different industries, but there are also vendors that offer industry-specific software.
General-purpose load planners
Most tools on the market focus on loading pallets, truck trailers, and standard shipping containers, rarely covering air transportation.
Load planners comparison
EasyCargo is a very user-friendly load planning tool with broad functionality and open API documentation for enabling integration with other systems. Their APIs are available as REST service over HTTP/HTTPS protocol.
Load Calculator by SeaRates is a simple application to “optimize stuffing” inside trucks or containers. It’s available in 3 options: online with unlimited access, web-integration on your website under white label, and API solution. More details are available upon request.
CargoWiz by SoftTruck is another easy-to-use cargo calculator built to optimize truck, pallet, and container loads. It’s enhanced with a Container Advisor feature that offers recommendations on the optimal container mix for your load.
CubeMaster by Logen Solutions is a comprehensive load optimization platform that works with multiple vehicle types and load rules. It offers a wide range of editions, from simple pallet load optimization to more advanced and full-featured versions.
CubeMaster has the Excel/CSV Import Wizard to import load lists from Excel or CSV files and the External DBMS Import Wizard to access external databases such as MS SQL, ORACLE or DB2, and bring in orders from your TMS, WMS, or ERP.
CubeMaster External DBMS Import Wizard
An online version is available -- CubeMaster Online. It also offers 3 sets of APIs to establish integration with other software systems: Database web service to upload information from your DB, Load Calculation web service to send the load data to and from the calculation engine, and Archive web service to download created load plans into your system.
Multi-modal load planners
Multi-modal shipping involves several modes of transportation and requires software that supports a wide range of containers for air, sea, rail, and land transportation, as well as safety standards and other constraints.
GOLDesp Load Planner was created as a commercially available module of ICODES, a military multi-modal load planning tool. It’s used to support freight movement by land, air, or sea.
MercuryGate is a popular TMS provider, also supporting multimodal transportation and offering a load planner as one of its modules.
Aviation load planners
Weight and balance are crucial for aircraft. There are strict weight restrictions and when planning loads, the weight of crew and sometimes passengers has to be considered. Also, cargo has to be distributed in such a way that the center of gravity is maintained throughout the flight.
CHAMP’s Weight & Balance is a load planning tool specially designed for aircraft. It’s fully compliant with Civil Aviation Authorities and IATA standards to ensure flight safety.
S4A Smart LOAD application also helps airlines automate load planning activities and reduce fuel costs by producing the optimal center-of-gravity calculations.
Vessel stowage planners
Today, ships carry huge amounts of varied cargo making accurate load planning essential to ensure optimal space usage and safe transportation.
StowMan solution by Navis helps shipping companies and terminals to efficiently manage their cargo operations. Its big advantage is the direct connection to the industry-leading MACS3 Loading computer system.
AMT Marine Software has a range of ship planning products depending on the type of freight shipped: RoRo cargo, general cargo, oversized and overweight cargo, etc.
AMT Marine Software interface
Solverminds’ Stowage Optimizer N Analytics Assistant (SVM SONATA) is another tool used to optimize vessel space utilization.
Implementing load planning software
There are 3 main approaches to implementing technologies that will help you with assembling your loads.
Part of TMS. Major providers of TMSs offer load optimization functionality out of the box, so if your business involves shipping goods on a regular basis, it might be worth getting a comprehensive tool that will cover most of your needs. In this case, all the modules will be well-integrated, but the range of features might be more limited than in specialized platforms.
Separate solution. If your business specifics don’t require a complex TMS, or the system you’re currently using doesn’t have load planning capabilities, you can choose one of the stand-alone solutions available on the market. We listed some options above, as well as features that we recommend considering when choosing the best fit for your business. In case you decide to purchase an off-the-shelf product, you’ll need a tech specialist to integrate it with your existing software and establish proper data exchange.
Custom development. Every business is different, so it might happen that you’re unable to find the right software to satisfy your specific needs. If so, it’s worth considering building a custom solution that will perfectly meet all the unique requirements of your business, help you streamline your operations, and increase your overall efficiency.
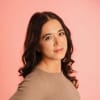
Maria is a curious researcher, passionate about discovering how technologies change the world. She started her career in logistics but has dedicated the last five years to exploring travel tech, large travel businesses, and product management best practices.
Want to write an article for our blog? Read our requirements and guidelines to become a contributor.