This is a guest article by IT service provider Asim Rahal
Supply chains involve complex webs of interconnected processes. Pull one thread, and the cascading effect of that change can unravel the entire chain. Given the relatively low margins supply chain stakeholders have to deal with, efficiency has always been a top priority, and the current supply chain crisis certainly isn’t making things easier.
It should thus come as no surprise that automation, delivered via technological innovation, has found a home in multiple supply chain functions. The most promising of these innovations is Robotic Process Automation or RPA.
RPA is already changing the healthcare sector and has implementations in insurance operations. Here's how it is set to change supply chain management in 2022.
Tasks that do not need specialized knowledge or insight are excellent fits for RPA. This is in contrast to cognitive automation, where technology needs a knowledge base and brings context and other human-like attributes to task execution. Unlike cognitive automation that seeks to replace or minimize humans in the decision-making chain, RPA aims to increase the value that each human worker brings to the chain.
Whether it is in highly specialized but codified functions in certain sectors or general functions that can be repurposed, RPA increases efficiency making it an ideal fit for modern supply chains.
First, there's the issue of data silos. Every stakeholder in the supply chain owns their part of the whole dataset. Thanks to proprietary knowledge issues, sharing this data for analytics is tough. This challenge has been cleared recently by fully integrated supply chains that bring visibility from sourcing to final delivery, often with the assistance of APIs.
However, data volume remains a challenge. Which segments of data are relevant for analytics, and when can those data sets be ignored? Data scientists and other stakeholders make these decisions every day. However, they also often find themselves burdened with tasks such as data cleaning, formatting, and preparation.
For instance, a data scientist tasked with determining the best route for a shipment must manually gather data from different sources, reformat these datasets to ensure uniformity, upload the data to a central analytics database, and examine these datasets to get rid of duplicates. There's hardly any time left for analysis.
RPA removes these hurdles, creating additional availability for humans to engage in more value-added work. The resulting ROI that stakeholders achieve is significant, even if the dollar value isn't readily apparent.
A good example of RPA's value addition is international trade transaction processing. A typical transaction involves 35 documents with 25 parties who need to remain compliant with over 600 regulations and 500 trade agreements. While transaction processing is complex, it is a codified, repetitive task more suited to RPA than a human being who can exert creativity.
RPA's benefits thus impact the entire supply chain thanks to the time it frees up.
Supply chain analytics is widely used, but these powerful platforms are powered by humble RPA systems. RPA technology, in the form of fixed procedures and codified routines, collect, clean, and format data, giving powerful analytics solutions a great base from which to begin. Data silos are eliminated, and stakeholders can rest assured that they're seeing the entire world of data under their purview.
RPA is also embedded in optical scanners that recognize goods on as many as six axes. These scanners feed data to broader warehouse management systems that define conveyor directs, guide vehicle paths, and camera lanes for drones. As such, they're directly connected to robots that work along defined lanes, bringing goods for packaging or storage. These physical robots are also excellent examples of RPA-powered devices in the modern supply chain.
Some companies are using robots to pick goods for order fulfillment as well. Picking is a repetitive task since the picker receives all relevant information regarding the item to be shipped. A robot can execute this task quickly and eliminate errors that occur in manual processes due to fatigue.
Advanced technology such as smart glasses is being trialed extensively in warehouses these days. These glasses direct wearers to inventory locations and reduce time spent searching for an item. Data provided by RPA systems power such augmented reality devices and create a more efficient warehouse.
In such situations, IoT devices alert relevant stakeholders, and mitigative action is taken. The data transmitted during this scenario can also automatically be formatted and stored for future analysis. Furthermore, it can be enriched by tagging it to datasets that describe the reasons for improper storage.
When viewed as a whole, these datasets can point to possible issues with vendors or supply chain processes. RPA can smooth the analytics function with the insights that eliminate clerical roadblocks like improper data formatting or siloed data stores.
Storing, relating, and retrieving these datasets manually can lead to potential errors thanks to the volume of data with which stakeholders contend. Instead, outsourcing this codified task to an RPA engine will create room for human employees to add value. For instance, if the customer requests changes, a human employee can override certain portions of the process and deliver an agile and efficient ordering experience.
As a consequence, RPA in this case allows stakeholders to build more flexible OM processes and potentially increase revenues through stronger customer relationships. Closely related to this use case are returns handling and after-sales follow-ups. In both cases, customers directly feed the system with valuable data signals.
In such scenarios, automating as much of the process as possible and freeing up time for a human agent to bring context to unstructured data will give stakeholders a leg up over the competitors.
Data integrity and value addition are constants throughout these use cases. They highlight the value RPA can add to complex processes and, counterintuitively, create more flexibility via automation.
An incurable evangelist of cloud security, data protection and cyber risk awareness, Asim Rahal is a Detroit-based independent IT service provider. You can reach Asim via Twitter: https://twitter.com/asimrahal
Want to write an article for our blog? Read our requirements and guidelines to become a contributor.
Supply chains involve complex webs of interconnected processes. Pull one thread, and the cascading effect of that change can unravel the entire chain. Given the relatively low margins supply chain stakeholders have to deal with, efficiency has always been a top priority, and the current supply chain crisis certainly isn’t making things easier.
It should thus come as no surprise that automation, delivered via technological innovation, has found a home in multiple supply chain functions. The most promising of these innovations is Robotic Process Automation or RPA.
RPA is already changing the healthcare sector and has implementations in insurance operations. Here's how it is set to change supply chain management in 2022.
What is RPA?
RPA is often confused with other technological advances. Briefly, Robotic Process Automation mechanizes repetitive, clerical, and time-intensive tasks that humans execute in complex processes. For instance, data entry in a supply chain process is a prime candidate for RPA, since it frees the human worker to conduct value-added work.Tasks that do not need specialized knowledge or insight are excellent fits for RPA. This is in contrast to cognitive automation, where technology needs a knowledge base and brings context and other human-like attributes to task execution. Unlike cognitive automation that seeks to replace or minimize humans in the decision-making chain, RPA aims to increase the value that each human worker brings to the chain.
Whether it is in highly specialized but codified functions in certain sectors or general functions that can be repurposed, RPA increases efficiency making it an ideal fit for modern supply chains.
The benefits of RPA for modern supply chains
Modern supply chains are data-gathering machines but deriving insights and strategic value from this data can be a challenge. IoT devices are embedded in every part of the supply chain, whether in machines on a manufacturer's production line to data loggers that power supply chain quality assurance processes. While the datasets are huge, getting them to talk to each other is tough.First, there's the issue of data silos. Every stakeholder in the supply chain owns their part of the whole dataset. Thanks to proprietary knowledge issues, sharing this data for analytics is tough. This challenge has been cleared recently by fully integrated supply chains that bring visibility from sourcing to final delivery, often with the assistance of APIs.
However, data volume remains a challenge. Which segments of data are relevant for analytics, and when can those data sets be ignored? Data scientists and other stakeholders make these decisions every day. However, they also often find themselves burdened with tasks such as data cleaning, formatting, and preparation.
For instance, a data scientist tasked with determining the best route for a shipment must manually gather data from different sources, reformat these datasets to ensure uniformity, upload the data to a central analytics database, and examine these datasets to get rid of duplicates. There's hardly any time left for analysis.
RPA removes these hurdles, creating additional availability for humans to engage in more value-added work. The resulting ROI that stakeholders achieve is significant, even if the dollar value isn't readily apparent.
A good example of RPA's value addition is international trade transaction processing. A typical transaction involves 35 documents with 25 parties who need to remain compliant with over 600 regulations and 500 trade agreements. While transaction processing is complex, it is a codified, repetitive task more suited to RPA than a human being who can exert creativity.
RPA's benefits thus impact the entire supply chain thanks to the time it frees up.
Examples of RPA technology revolutionizing logistics operations
RPA is finding its way into the supply chain through a wide range of innovative solutions. One of the earliest applications to appear was the multishuttle system. These systems are a part of larger automated storage and retrieval systems. They're tasked with moving goods from pallets to shelves and back. They eliminate the need for a human to physically haul goods around warehouses and store them for retrieval.Supply chain analytics is widely used, but these powerful platforms are powered by humble RPA systems. RPA technology, in the form of fixed procedures and codified routines, collect, clean, and format data, giving powerful analytics solutions a great base from which to begin. Data silos are eliminated, and stakeholders can rest assured that they're seeing the entire world of data under their purview.
RPA is also embedded in optical scanners that recognize goods on as many as six axes. These scanners feed data to broader warehouse management systems that define conveyor directs, guide vehicle paths, and camera lanes for drones. As such, they're directly connected to robots that work along defined lanes, bringing goods for packaging or storage. These physical robots are also excellent examples of RPA-powered devices in the modern supply chain.
Some companies are using robots to pick goods for order fulfillment as well. Picking is a repetitive task since the picker receives all relevant information regarding the item to be shipped. A robot can execute this task quickly and eliminate errors that occur in manual processes due to fatigue.
Advanced technology such as smart glasses is being trialed extensively in warehouses these days. These glasses direct wearers to inventory locations and reduce time spent searching for an item. Data provided by RPA systems power such augmented reality devices and create a more efficient warehouse.
RPA use cases in the supply chain
Beyond the examples discussed above, RPA has numerous applications across the supply chain. One of its most relevant uses lies in automating and integrating data transmission across multiple functions.Integrated data transmission
Condition monitoring provides a good example of this use case. If sensitive shipments are not in ideal storage conditions, everyone from the manufacturer to the shipper face losses.In such situations, IoT devices alert relevant stakeholders, and mitigative action is taken. The data transmitted during this scenario can also automatically be formatted and stored for future analysis. Furthermore, it can be enriched by tagging it to datasets that describe the reasons for improper storage.
When viewed as a whole, these datasets can point to possible issues with vendors or supply chain processes. RPA can smooth the analytics function with the insights that eliminate clerical roadblocks like improper data formatting or siloed data stores.
Order management
Order management touches everything in the supply chain, and it epitomizes how complex processes can become. Customers provide multiple data points during the order process, and everyone from the manufacturer to the logistics provider must take them into account. For instance, shipping speed and location are invaluable data sources during the OM process.Storing, relating, and retrieving these datasets manually can lead to potential errors thanks to the volume of data with which stakeholders contend. Instead, outsourcing this codified task to an RPA engine will create room for human employees to add value. For instance, if the customer requests changes, a human employee can override certain portions of the process and deliver an agile and efficient ordering experience.
As a consequence, RPA in this case allows stakeholders to build more flexible OM processes and potentially increase revenues through stronger customer relationships. Closely related to this use case are returns handling and after-sales follow-ups. In both cases, customers directly feed the system with valuable data signals.
Returns and after-sales handling
Return handling can be fully automated thanks to clearly defined processes. However, after-sales follow-ups generate unstructured data that require human intervention to spot value.In such scenarios, automating as much of the process as possible and freeing up time for a human agent to bring context to unstructured data will give stakeholders a leg up over the competitors.
Data integrity and value addition are constants throughout these use cases. They highlight the value RPA can add to complex processes and, counterintuitively, create more flexibility via automation.
Implementing an RPA program in your supply chain
Step one: Define goals and business benefits
While the benefits of RPA are massive, stakeholders must avoid rushing in without a plan. The first step to successfully implement RPA is to define business-oriented goals and metrics that can track success or failure. For instance, how will a company measure an increase in efficiency? Will it be via hours saved or quantified by dollar amounts?Step two: Seek executive buy-in
Once these essential terms have been defined, project stakeholders must prepare for an optimal launch. It's usually best to begin with a pilot project equipped for success since this guarantees executive buy-in. Any RPA project that lacks full higher management backing will fail, since it requires cross-organization integration to succeed. For instance, automating data collection works best when scaled across multiple processes.Step three: Define change management processes
As the RPA program's scope expands, challenges will arise, and processes will require modification. Maintaining a detailed changelog and recording the reasoning behind changes are essential tasks for the project team to execute. By maintaining an audit trail, future decision-making becomes clear, and the company can realize scalable gains.Step four: Create a center of excellence
The final step is to build an RPA center of excellence within the organization. This team must maintain a standard set of process parameters and be the reference point for anything to do with RPA. The center of excellence must also evaluate future challenges such as technical integration with cognitive technology.Complex but necessary
On the surface, RPA looks like a bunch of automated processes wheeling away in the background. However, they're far more critical to supply chain efficiency than they first look. RPA processes act as the plumbing to more complex technological supply chain elements. Any organization that takes the time to implement it will undoubtedly realize massive efficiency gains in its supply chain.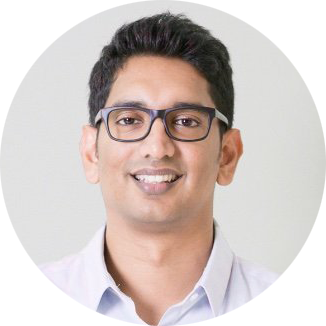
Want to write an article for our blog? Read our requirements and guidelines to become a contributor.