“Control towers are the artificial intelligence (AI) of supply chain. Everyone wants to have it, but nobody quite knows how it works.”
Christian Titze, vice president analyst at Gartner. Source: Supply Chain Dive
Over the last few years, global supply chains have been so severely disrupted – but also enhanced -- with cutting-edge technologies. And today, supply chain managers face more challenges – and more opportunities -- than ever. Leading executives focus on building resilient and intelligent supply chains that can withstand the turmoil due to data-based proactive decisions. Let’s look at what they say in recent surveys.
- According to the PwC 2023 Digital Trends in Supply Chain Survey, 86 percent of respondents believe they should invest more in technology to identify, track, and measure supply chain risk.
- The annual IHS Markit Supply Chain Survey Report found that 63 percent of companies don’t have sufficient technology to approach their top priority optimization strategy, i.e., spend analytics (the situation within other strategic areas is similar).
- In 2021, 77 percent of the McKinsey survey of global supply chain leaders’ respondents named supply chain visibility as the most important area to digitize.
These and other numbers show that supply chain managers want more visibility into what’s going on at every stage – and that the right technology is essential to make it happen. So that’s what we’re going to discuss today: What exactly is supply chain visibility and how can a control tower help achieve it?
What is supply chain visibility and why is it important?
Supply chain visibility is basically the detailed knowledge of every operational activity as it entails the ability to track and trace all the goods (inventory, parts, raw materials, etc.) throughout every stage and across all the tiers of the supply chain. Besides, it means having information about your suppliers, customers, carriers, and other partners, as well as about your internal processes all along the line.
If we speak about end-to-end visibility, we mean that we should be able to have a granular view of all the main components of a supply chain:
- transportation – which entails control over the actual delivery process, tracking shipments, predicting ETA, etc.;
- warehousing and fulfillment – which oversees the storage, packaging, and order management activities;
- inventory management – which focuses on maintaining optimal stock levels;
- procurement and production planning – which involves predicting demand and adapting manufacturing strategies;
- distribution and customer management – which encompasses building effective sales strategies and keeping customers satisfied; and
- supplier management – which entails vendor assessment and vetting, as well as contract management.
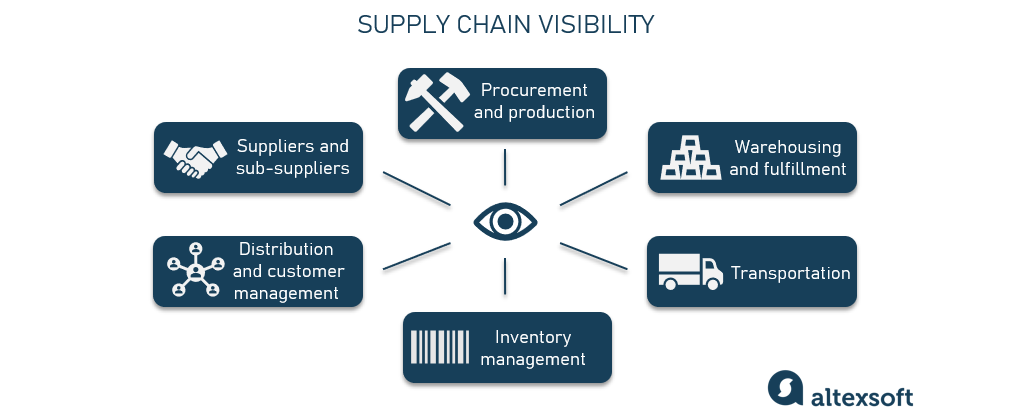
Supply chain visibility main components
Supply chain visibility is crucial -- if you don’t have it, it’s like walking blindfolded. In today’s highly volatile and competitive environment, you can’t successfully manage a business without having a total understanding of what’s happening in and around your company.
Having complete, end-to-end visibility into your supply chains will allow you to increase resilience, manage disruptions, reduce risks, and avoid loss. Specifically, you’ll be able to
- trace your inventory across multiple supplier tiers and define potential risks;
- see inventory-related problems like stockouts, overstocking, or shrinkage;
- track in real time how goods move along the supply chain up until they reach the end customer;
- monitor KPIs and identify operational inefficiencies such as time delays or unnecessary spending at any stage (procurement, warehousing, transportation, etc.);
- increase customer satisfaction by giving real-time status updates; and so on.
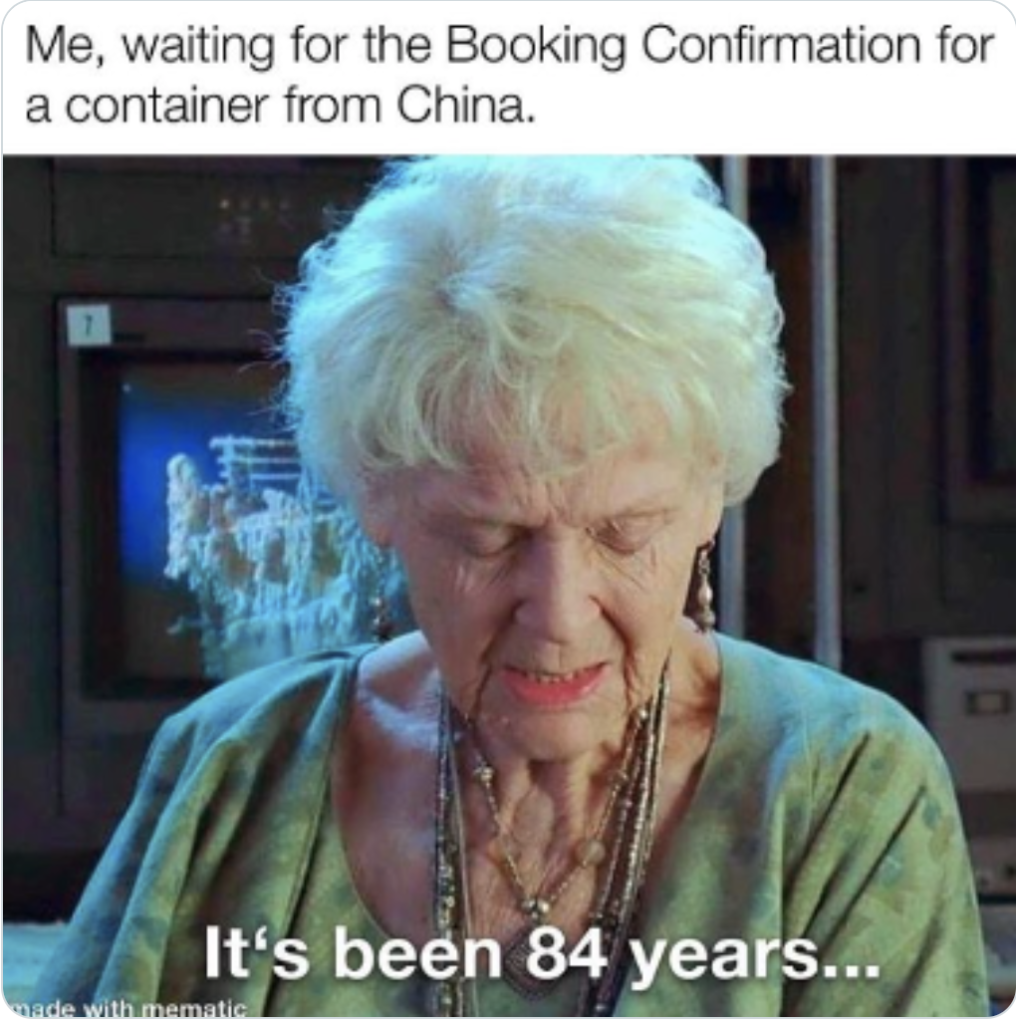
Timely updates are much appreciated. Source: DCPerform
Supply chain visibility vs traceability, transparency, and mapping
Supply chain visibility is tightly intertwined with traceability, transparency, and mapping. Let’s define terms to get a better picture.
Supply chain traceability is about tracing the complete lifecycle of goods. It means having information about their origin, journey, ownership, certifications, etc., from the very beginning of the supply chain. So we can say that traceability is one of the components of visibility.
Supply chain transparency relates to disclosing information to customers and other stakeholders – or deciding what you’ll be transparent about. It’s up to you which information to share, how, with whom, how often, and so on. But of course, you can only share data you have yourself – so higher visibility leads to higher transparency.
Supply chain mapping means gathering information about your suppliers and partners and creating a map of your business network. This way, you have a visual representation of the flow of goods and cash, as well as interrelationships between your business connections. So mapping is an important process that results in greater visibility.
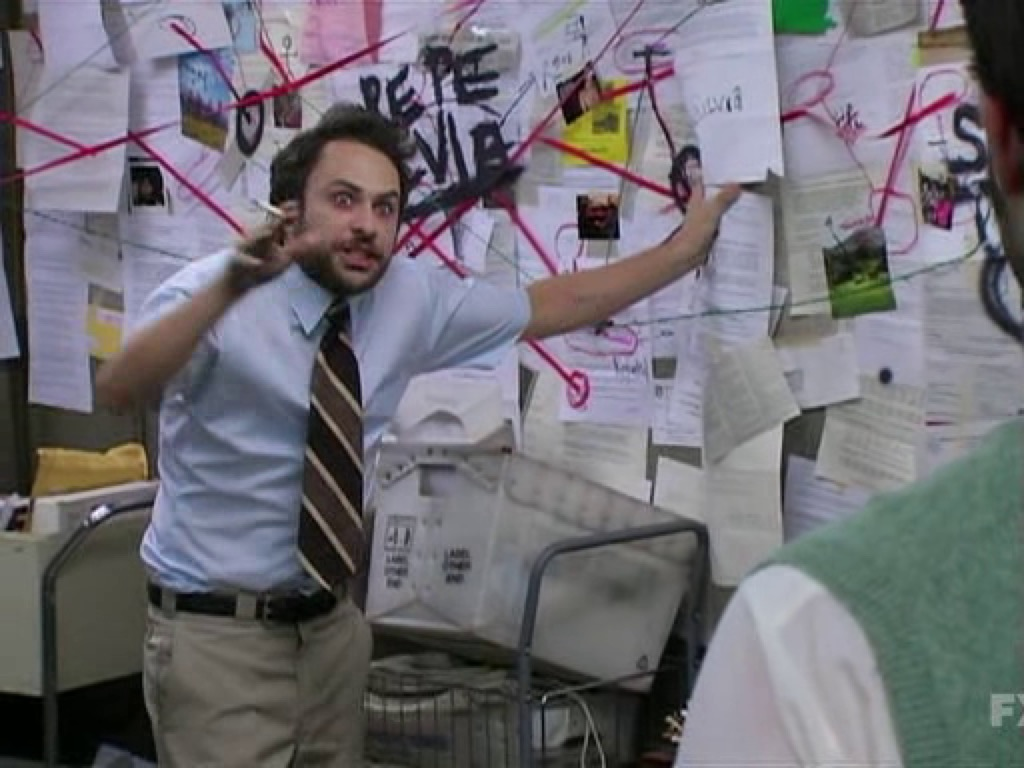
This is what your supply chain mapping process can look like… But we know a better way
All that said, how can you achieve better visibility into your supply chains? Obviously, it’s all about collecting data from various sources, both external and internal, which is possible with specialized technologies.
Supply chain visibility software
Supply chain visibility software enables real-time tracking of goods and materials throughout the entire supply chain. It also often includes analytics, reporting, and forecasting capabilities.
Such solutions typically come preintegrated with numerous ERPs, transportation management systems (TMSs), warehouse management systems (WMSs), and supply chain management (SCM) platforms – as well as telematics/ELD providers. These established connections allow them to easily integrate into most supply chain IT ecosystems and facilitate data exchange between parties, whether you want to track your own fleet or third-party logistics providers.
Many visibility platforms also offer global container/vessel/rail/air cargo tracking and deliver multimodal visibility, which comes in handy for companies dealing with international logistics.
The ability to track shipments is crucial as it allows supply chain managers (shippers, freight forwarders, 3PLs, etc.) to see where freight is in real time and what the ETA is, share this information with customers, monitor and analyze fleet/carrier performance, and much more. You can set up automated alerts and status updates to always be on top of your deliveries.
Some of the most popular supply chain visibility products today are
Supply chain visibility platforms play an important role in logistics management… But they can’t deliver the end-to-end visibility we spoke about earlier as they mostly focus on the transportation aspect. And if you as a supply chain executive want to have a detailed view of all operational activities and support your decision-making with comprehensive data analytics, you need a more advanced solution.
Supply chain control tower and its benefits
A supply chain control tower (SCCT) is an integrated IT system that collects real-time data from all the functional areas of a supply chain (from strategic planning and procurement to last-mile delivery and reverse logistics), aggregates it in a central storage/analytical hub, and enables control over all departments and processes.
Due to extensive usage of connected IoT devices and advanced processing technologies, SCCTs not only gather data and build operational reports but also create predictions, define the impact of various macro- and microeconomic factors on the supply chain, and run what-if scenarios to find the best course of action.
It’s important to note that an SCCT isn’t a specific piece of software but rather a suite of interconnected tools. Often, such an ecosystem is built on top of the ERP or SCM. In other words, visibility software can serve as a basis, but it’s only a part of the SCCT platform.
Previously, control towers were seen as multifaceted dashboards to monitor performance. Sometimes, they were designed to control a particular aspect of a supply chain. But now it becomes possible to break down the siloes and orchestrate all the key workflows we described above.
Depending on a company's business focus, its supply chain structure, and its IT ecosystem, an SCCT can be tailored to deliver greater visibility into a specific aspect. For example, it can be enhanced with an RTLS to ensure accurate asset tracking in a warehouse.
The ultimate goal of an SCCT is to support efficient, data-based decision-making, planning, and risk management, as well as quick and effective reactions to disruption. A well-designed SCCT must allow you to view all operations, plan, and execute – all in the same system.
Okay, if put very simply, we can say that a control tower can show us what’s happening along our supply chains at any given moment, why it’s happening, what we can expect to happen next, what we should do about it, and what happens if we change something. So it takes us from merely seeing what’s going on (the visibility level we discussed) to understanding and acting upon data.
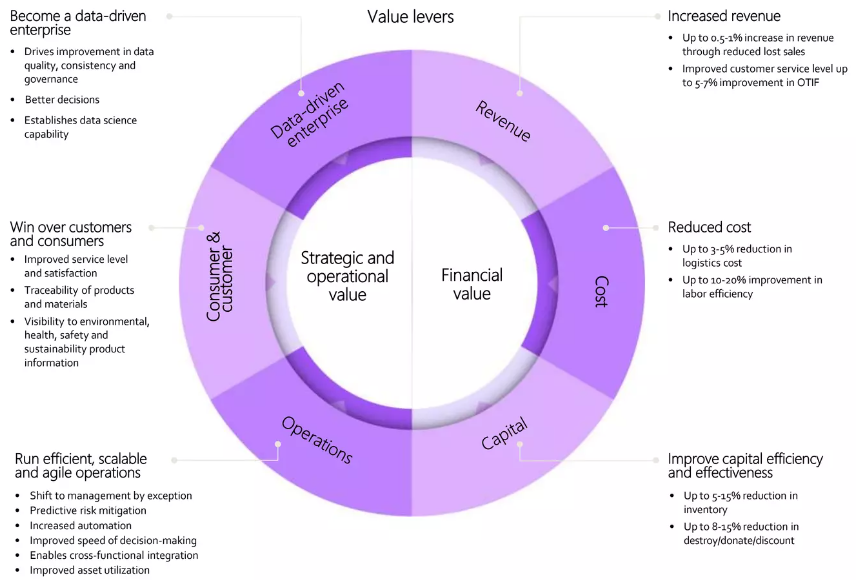
The value of implementing an SCCT. Source: Accenture
Accenture calculated that some tangible benefits of SCCT implementation include
- revenue increase by up to 1 percent through reduced lost sales,
- logistics cost reduction by 3-5 percent,
- labor efficiency improvement by 10-20 percent,
- 5-15 percent reduction in inventory, and
- 8-15 percent reduction in destroy/donate/discount.
Supply chain control towers bring significant value by providing end-to-end visibility, predictive analytics, decision support, automation, and so on. As a consequence, supply chain executives can streamline the movement of goods along the chains, cut costs, and increase customer satisfaction.
Supply chain control tower architecture: main components, integrations, and data sources
As we mentioned, an SCCT is typically comprised of multiple components that handle various aspects of supply chain management. Let’s look closer at what’s under the hood and list the main components, integrations, and data sources.
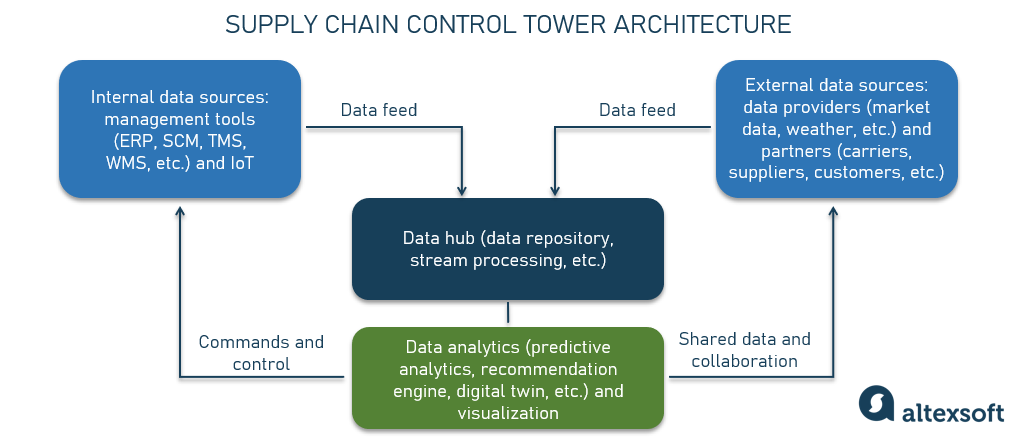
Supply chain control tower architecture
Internal data sources
The SCCT must be able to get data from all internal processes as well as give maximum control over them. It means that it must have access to the systems we commonly use to manage our separate supply chain links such as
- manufacturing software,
- procurement software,
- order management system,
- inventory management software,
- TMS,
- WMS,
- yard management system,
- retail software,
- CRM, and so on.
The readings from IoT sensors and other connected devices (e.g., installed for tracking or condition monitoring purposes) also contribute to end-to-end visibility.
External data sources
To deliver comprehensive visibility and make accurate forecasts, your SCCT must collect data from external sources. Those can include the systems of your suppliers, customers, or other partners that you can connect to (e.g., carriers, 3PLs, freight forwarders, etc.) as well as third-party data providers (e.g., market data, weather, maps, social media, etc.).
A central data hub
To integrate all the information, you need a centralized repository that stores both structured and unstructured data.
In a nutshell, structured data is organized in a predefined format and typically lives in tables with rows and columns (for example, order tables with such information as SKUs, quantities, dimensions, contact details, etc.).
Meanwhile, unstructured data doesn’t have a predefined structure and comes in a wide variety of forms such as audio, imagery, texts, etc. (in supply chains some examples can be scans of handwritten BOLs, pictures of goods, CCTV records, or customer reviews in social media).
To store all this diverse information, you’ll have to utilize a centralized data repository such as a data warehouse or data lake. You can read the details on them in the linked articles, but in short, data warehouses are mostly used to store structured data and enable business intelligence, while data lakes support all types of data and fuel big data analytics and machine learning.
You can also consider a cloud data lakehouse as an option since it addresses the limitations of the aforementioned repository types and works with various data workloads.
To enable real-time analytics, the central data hub also must support data streaming. As opposed to batch data, streaming data is one that continuously flows and has to be processed on the fly. For example, you’ll deal with real-time data streams if you want to adopt predictive maintenance which requires constant condition monitoring or implement an RTLS system to continuously track your handling equipment and other assets.
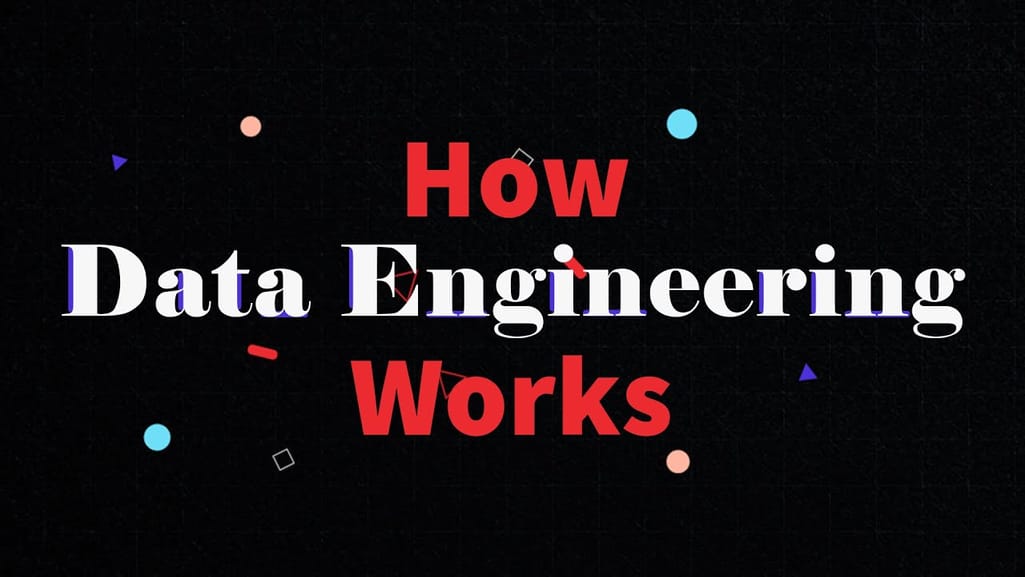
To get a better picture, check out a short explainer of what data engiineering is about
Data analytics
Now that we have all this data, we can finally work on the actual witchcraft. So here are some of the reasons control towers are actually being developed.
Predictive analytics is about detecting trends and coming up with accurate forecasts of future events. That’s what actualizes such important processes as demand forecasting, predictive maintenance, risk assessment, and much more. Analytics results are then visualized with the help of real-time, interactive dashboards and reports. They can also be shared with departments and partners to foster collaboration.
Digital twins are the virtual replicas of supply chains (or other processes/objects) that are connected to all your data sources and that help monitor performance, run simulations and impact analysis, test various scenarios before implementing them, and much more.
Recommendation engines compare numerous scenarios and define an optimal course of action based on the available data and created forecasts. Such prescriptive analytics technology can solve some common logistics problems such as routing or tendering – and also support decision-making at all levels, from strategic planning to operational reactions to disruption.
All these and other technologies work together in synergy to bring clarity to supply chain management and enable effective decision-making. The ultimate control tower development stage is maximum automation, meaning that the system autonomously analyzes incoming data, comes up with a solution or reaction, and executes it without any need for human intervention.
Now that you have an idea of the SCCT structure, let’s get more practical and talk about how to approach its implementation.
Supply chain control tower implementation
If you set your mind to achieving such holistic control over your supply chain, the important decision you’ll have to make is whether you buy an off-the-shelf product or develop your own.
To buy or build?
The tricky part here is that you won’t be able to find a ready-made solution on the market that perfectly suits your unique business requirements. All businesses are different so if you want a turnkey solution, you’ll have to partner with a specialized software provider who'll help you build the entire SCCT infrastructure. Such a project will involve customizing their product to your needs and integrating selected software in your IT environment.
Meanwhile, developing a multifaceted, proprietary, bespoke platform guarantees you maximum customization and correspondence to your needs. However, the big drawback of such an approach is obviously its price and duration as it can last for years and cost a fortune. Besides, you'll need to engage a team of skilled data specialists (data engineers, data scientists, etc.) to develop all the data architecture and analytics solutions.
The sensible compromise here can be gradually enhancing your existing system with additional tools and advanced capabilities. This way, you can keep working with the interface you’re used to and stretch investment over time, but concurrently, start fixing the most problematic areas at once and eventually get a comprehensive control tower platform.
This approach has many advantages, but if you think that getting a ready-made product is a better way for you, let’s take a look at what the market offers so that you can check existing platforms and get a fuller understanding of your options.
Supply chain control tower software
Here’s a list of leading control tower providers according to the Control Tower Technology Value Matrix by Nucleus Research.
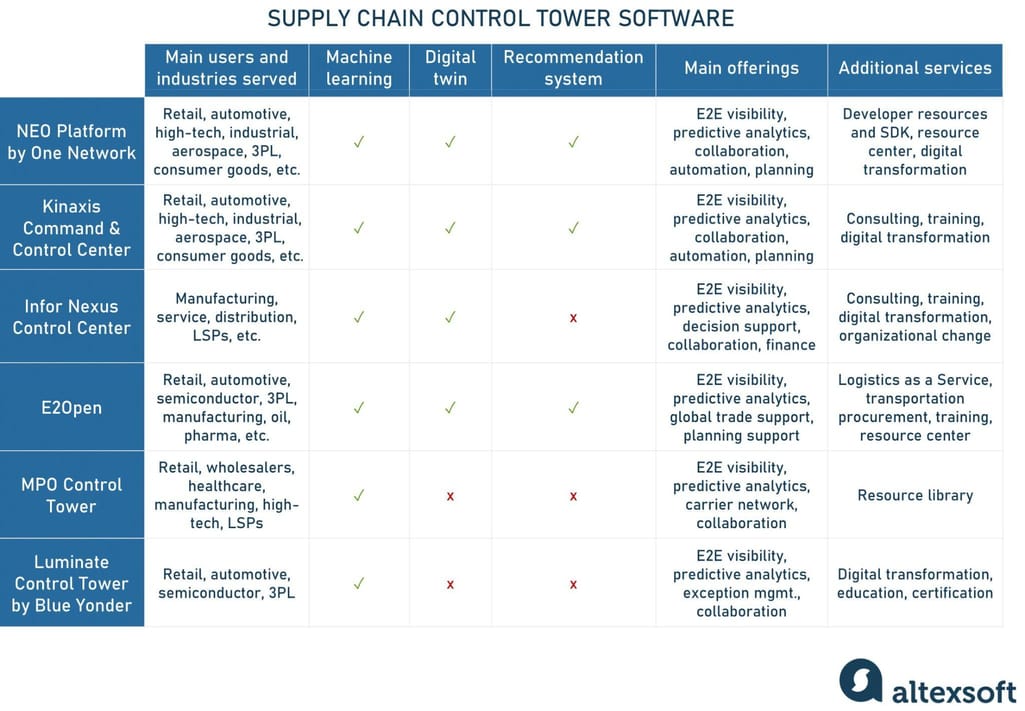
Control tower software compared
One Network Enterprises has created an intelligent AI/ML-based NEO Platform capable of autonomous decision-making and prescriptive analytics across the entire supply chain. In addition to providing end-to-end visibility, they claim to offer such tangible benefits as
- 90 percent reduction in shortages/stockouts,
- 75 percent reduction in expediting costs,
- 100 percent and more increase in inventory turns, and
- 100 percent increase in on-time shipments.
Kinaxis is another renowned industry leader that offers an SCCT that enhances planning, collaboration, and control over operations. There are also a number of extensions, for example, the ML-based Self-Healing Supply Chain add-on “automatically detects, corrects, and heals inaccurate planning inputs like lead times and yields.”
Kinaxis’ customers report the platform’s usefulness for planning and analytics purposes, as well as increasing sustainability, managing disruptions, improving agility, and so on.
Infor is a provider of ERP solutions for various industries that offers the Infor Nexus platform for “multi-enterprise supply chain orchestration and optimization.” Including data from key supply chain partners, Infor uses knowledge graphs to map numerous supply chain management aspects (parties, places, products, etc.) into the digital twin.
As a result, users get multiparty connectivity, predictive alerts, prescriptive recommendations, and collaborative execution.
E2open specializes in logistics software solutions. Its e2net platform is an open partner network that helps you “connect all trading partners and logistics providers across all tiers and ecosystems, then focus on the larger picture of opportunities and risks that you and your partners tackle together.” It also leverages digital twin technology to enhance visibility and support decision-making.
By the way, e2open also offers Logistics as a Service if you want to outsource your transportation activities.
MPO’s multiparty orchestration software supports the entire order management cycle from planning to fulfillment to delivery. It has a large network of integrated carriers, offers vast automation options, and delivers a granular view into supply chain processes and costs. In 2022, it was acquired by Kinaxis.
Blue Yonder provides a Luminate Control Tower platform. It leverages AI and ML to discover trends and insights from real-time data, empowering informed decision-making. The platform delivers end-to-end visibility across the supply chain, enhances multiparty collaboration, helps predict and resolve disruptions, and recommends optimal actions.
Important aspects to consider
When choosing IT solutions, the main focus is commonly put on the balance of capabilities and price. However, here are some more essential aspects to consider if you want your supply chain control tower to deliver maximum value.
Integrations. Seamless interconnectivity lies at the core of an effective SCCT because... well, it’s all about smooth data exchange throughout the entire IT ecosystem. So it’s crucial to build integrations between all the elements of an SCCT (e.g., WMS, IMS, TMS, CRM, BI, etc.). However, it’s easier to accomplish if you select products that have prebuilt integrations out of the box.
Third-party data providers. It’s related to the previous one, but we wanted to emphasize the importance of connecting to the external data sources we mentioned above. You can’t build accurate forecasts based only on internal information so check if your software provider has a diversified data feed or build such integrations yourself.
Automation. Automating repetitive routine tasks streamlines operations and increases efficiency. Look for automation opportunities (such as setting up status alerts or auto-reacting in response to various events), build intelligent, autonomous workflows, and make your SCCT platform work for you.
Analytics capabilities. As we said earlier, the sought-for profound level of visibility and decision support can only be achieved through implementing state-of-the-art technologies capable of advanced analytics – predictive and prescriptive.
Data security. As you start working with massive amounts of information, it becomes important to protect it from any unwanted actions, so make sure your software complies with data security regulations like GDPR.
Scalability. As your business scales, your SCCT platform must be able to handle the growing number of partners, transactions, and operations.
Balance. Visibility is pivotal, but when you deal with millions of different SKUs and thousands of suppliers, it’s impossible (or at least economically unprofitable) to cover each and every operation. And it’s okay if you don’t. What’s more important is to define your strategic priorities and focus on optimizing the most critical workflows.
Implementation challenges
Whether you choose to buy or to build, it’s a lengthy, complicated project demanding significant investment. Besides, there are a number of challenges that often arise during such endeavors.
Lack of skilled experts. You’ll obviously need a team of professional data engineers and other specialists to build and maintain such a platform.
Data siloes. You can only get visibility if you get access to data from both external and internal sources – and that can be a problem.
Poor data quality. Predictions are only as good as the data they’re based on, but getting sufficient, high-quality data can be challenging.
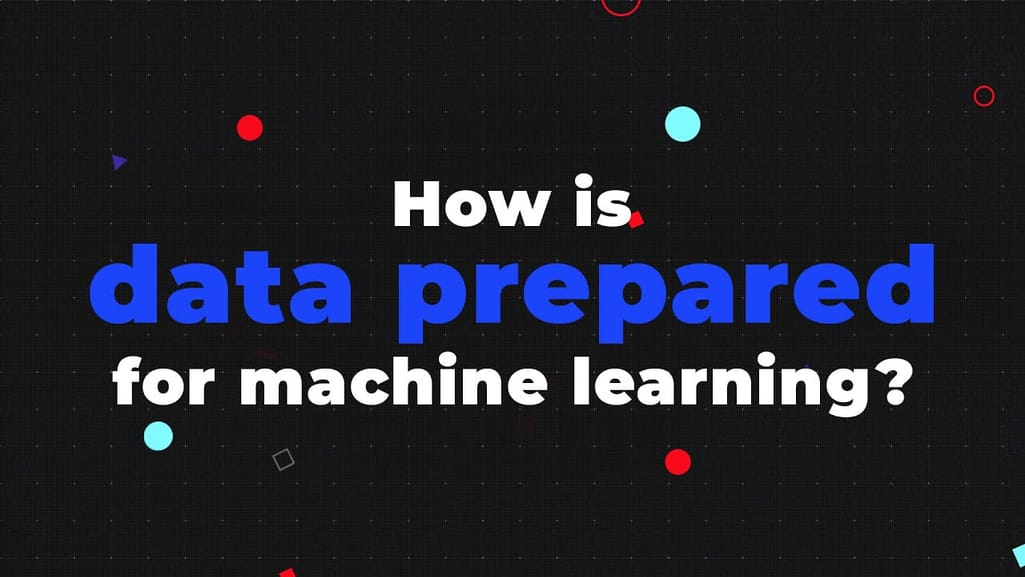
How to prepare data for machine learning
These pitfalls are common and can hinder your implementation project, but if you’re aware of them from the very beginning, you can come up with ideas on how to address them and take proactive steps. For inspiration, let’s take a quick look at some real-life case studies of implementing control towers.
Real-life control tower cases
Here are only a few examples of how digitization can help streamline supply chain processes and improve efficiency.
SAP control tower implementation results in reduced downtime and easier access to data
Schnellecke Logistics SE, an automotive industry logistics provider, partnered with SAP to create a control tower. Among many operational improvements, they witnessed fewer stops on the production line, a big deal given that 1 minute of downtime could cost up to €5,000.
The control tower also led to increased employee productivity and easier access to data, actionable insights, and predictive analytics. For example, it eliminated those 15-20 steps required to get the needed data, and a report that previously took two hours to generate became immediately available.
MPO control tower helps save costs and optimizes performance
Another example is GEODIS (which is also a global logistics provider) leveraging an MPO platform to bring significant savings to their customer. Advanced control tower capabilities (such as dynamic, multi-leg carrier selection, in-transit stock visibility, order-splitting and consolidation, and dynamic invoice matching) led to about 5 percent cost savings across logistics and billing, as well as overall efficiency gains. Increased visibility enabled optimization that resulted in about $1.5 million in annual savings.
IBM control tower reduces expenditure and enhances order management
IBM has built an SCCT based on its own suite of IT products to optimize its own supply chain which spans 170 countries. It allowed them to enhance resilience and handle disruptions so efficiently that even during the COVID crisis, they managed to deliver 100 percent of orders to their clients. Their demand sensing, risk management, decision support, and other integrated tools helped reduce supply chain costs by $160 million.
However, the scope of their digital transformation initiatives embraced not only implementing advanced technology but also developing a cultural shift to empower people and adjust operational workflows.
Where to start
Many leading software providers like Infor, IBM, or Kinaxis also offer consulting services to help their customers start off with tech and business improvements and build a roadmap to enterprise-wide transformation. Getting assistance from experts is a great way to approach digitization but if you want to go your own way, here are a few ideas on where to start.
Assess your existing environment. Look at your current practices, critical suppliers, data sources, revenue streams, and tech ecosystem. Define the primary vulnerabilities and areas that need improvement.
Define priorities. Trying to optimize all at once can be too big to swallow. As you have an understanding of your weak points, prioritize them to define the main areas to focus on.
Create a collaborative environment. You’ll have to break data siloes both within your organization and outside it. Explain the importance of data sharing and collaboration to employees and stakeholders and get their support for your digital initiatives.
Train staff and set up processes. As you implement new capabilities, make sure your staff understands their value and knows how to use the new systems. Cultivate the culture of data-driven operations. Encourage your workers to rely on analytics in planning and decision-making and to look for further automation and improvement opportunities.
An agile and resilient supply chain is only possible with end-to-end visibility, advanced analytics, and automation. Enhance your planning and execution with cutting-edge technology and reap the benefits of business growth, optimized workflows, and improved bottom line.
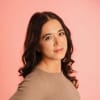
Maria is a curious researcher, passionate about discovering how technologies change the world. She started her career in logistics but has dedicated the last five years to exploring travel tech, large travel businesses, and product management best practices.
Want to write an article for our blog? Read our requirements and guidelines to become a contributor.