The recent Royal Bank of Canada (RBC) overview of global supply chains explicitly displays how bad port congestion currently is – and how it keeps getting worse. The study states that one-fifth of the global container ship fleet is stuck at various major ports. The turnaround time keeps increasing in all the biggest terminals of China, the US, and Europe.
Global business news channel CNBC created Supply Chain Heat Maps to track the levels of container terminal performance. For example, in the US, the situation in the Port of Oakland is the worst with vessels taking an average of six days to unload and load (import containers are waiting eleven days to get transported). The ports of Los Angeles and New York are not far behind.
In the first half of 2022, the main reasons for supply chain slowdown and port bottlenecks are China's battle with COVID that results in lockdowns, the Russian invasion of Ukraine, increased fuel prices, deficient terminal infrastructure, and inefficient terminal operations. And while you as a terminal manager might not have power over global problems, what you can do is optimize your operations and implement technology to streamline workflows and decrease processing time.
In this article, we describe the terminal operating software, its main features, possible integrations, and ways it can benefit port productivity. Note, that we’ll only talk about cargo terminals and won’t cover other port activities such as fishing, ferries, cruises, etc.
What are the main terminal operating problems?
All the cargo ports and terminals are different. They vary in size, freight types (e.g., bulk or container terminals), and location (sea or inland ports). However, we can roughly generalize that the main functions of most cargo terminals revolve around catering to
- vessels (discharge, repairs, refueling, etc.),
- freight (loading/unloading, storage, stuffing/stripping, etc.), and
- connected inland transportation (arrangement of cargo movement).
Understanding these key objectives allows us to highlight the common pain points of operating a cargo terminal throughout its key areas – the berth, the yard, and the gate.
Main terminal challenges
Disruptive vessel calls planning
On the vessel side, the challenge lies in scheduling berth windows, arranging loading/unloading equipment according to vessel ETAs, and communicating with the shipping line to synchronize operations.
It’s important to carefully arrange all the pieces of this puzzle, set up the optimal loading/unloading sequence, and exchange messages with the carrier’s system to maximize the operational efficiency. This process becomes even more complicated due to frequent vessel delays and other disruptions that lead to waste of time, fuel, and port resources, so operators have to timely react and reschedule berth and resource allocation. All of that becomes a herculean task without specialized software.
Inefficient yard space configuring
The yard is basically a large storage area in the terminal that has to be efficiently managed. The main complexities here include optimal cargo allocation, handling equipment and staff coordination, and truck movement organizing. Different storage areas have to be created and freight has to be allocated according to further operations. Since most terminals process thousands of containers (not to mention other cargo types) daily, orchestrating all these processes manually is barely possible.
Lengthy truck visits arrangement (appointment booking, permission granting, verification, etc.)
Another important terminal workflow is gate management. Incoming and outgoing vehicles have to be carefully monitored. Access permission can only be granted to authorized vehicles and according to the associated cargo details, which then has to be verified at the gate. But performing all the checks manually is too lengthy and error-prone. And when hundreds of trucks come in and out to deliver or pick up freight, it can easily cause bottlenecks, so this flow has to be properly arranged.
Complicated staff and equipment scheduling
Scheduling is always a problem, especially in large businesses with multiple operational units. In the terminal, staff and equipment schedules mainly depend on the vessel calls and truck visits. Connecting all of them together is hard in itself, and when inevitable disruptions like equipment failures or vessel/truck delays happen, everything becomes a hot mess.
Inefficient cargo tracking resulting in lost freight
Another problem is monitoring cargo flow within the terminal. Goods have to be tracked when they arrive, unloaded/loaded, transshipped, and stored, so that nothing gets lost in the terminal chaos – which unfortunately is not an uncommon situation.
Inaccurate billing that leads to lost revenue
Terminals perform thousands of billable operations daily for numerous customers. All the charges have to be accurately captured and added to corresponding invoices. If done manually, operators get buried under tons of paperwork – and still can’t avoid putting a foot wrong.
Data leakages in reporting and analytics activities
Terminal operators need to have full visibility into all facility activities. Some of the important KPI categories that have to be monitored are
- gate events and truck movements,
- terminal inventory,
- vessel movements,
- crane (and other equipment) productivity,
- yard utilization,
- demurrage and detention, and many more.
To create all these valuable reports, data has to be collected across all terminal departments. However, traditional organizations with siloed structures make data sharing very complicated, leading to information leakages and communication delays (which cause disruptions too). So, no reporting and holistic data analysis is possible without having all the data in one integrated system.
In today’s digital world ruled by data, your performance and competitiveness often depend on your technological level. So, let’s see how modern software can optimize your terminal operations.
The terminal operating system and its key modules
In a nutshell, the terminal operating system (TOS) is a digital platform that helps track and manage all the supply chain operations at the cargo ports and terminals. TOSs help coordinate all the terminal logistics elements (including vessels, trucks, cranes, trains, and port staff), track cargo movement, optimize asset usage, and analyze data to support decision-making.
Now, let’s take a deeper look into TOS functionality and its core modules intertwining.
TOS main modules
Berth management: planning vessel visits and predicting ETA
The maritime industry historically relies on the Electronic Data Interchange or EDI technology for information exchange (we’ll describe it in more detail further on). It’s required for effective berth management as well. Carriers or agents send the BERMAN or berth management message to the port that contains a request to moor, details of the call and vessel, berth requirements, and expected operations. Obviously, all this information can’t be received and processed without the integrated TOS.
That helps terminal operators to synchronize all the ship-related activities. A TOS helps schedule vessel visits, their moves between terminals (if necessary), and associated services, as well as coordinate tugboats and staff. If your terminal experiences significant tidal events, make sure your TOS offers dynamic tidal modeling to safely manage vessel movements.
Sometimes the ETA received from the shipping line isn’t exact, so terminals often make their own predictions regarding port calls timing. A common way to do it is by connecting to the automatic identification system (AIS) data source which allows users to track vessels in real time.
Yard management: arranging cargo movement and allocating terminal resources
Yard management generally refers to organizing the movement of cargo, handling equipment, vehicles, and staff in the yard of the warehouse, terminal, distribution center, or another facility. The TOS helps automate and streamline the yard operations we talked about earlier:
- defining areas for all types of cargo and operations (loading/unloading, transshipment, storage, etc.);
- allocating and scheduling staff (by creating convenient to-do lists) and equipment (including ARMG, ASC, forklifts, etc.) for all types of operations;
- monitoring equipment location (due to a so-called real-time locating system or RTLS, which we’ll talk about later), etc.
The TOS contains all the information on the incoming and outgoing freight and can automatically coordinate available equipment, staff, and space according to the cargo requirements and type of operation. And the load planning functionality helps configure your yard areas and arrange cargo in the most efficient way with optimal space usage, considering load constraints and further operations.
In addition, having a real-time view of all yard processes allows terminal operators to immediately react to any disruptions.
Freight management: cargo tracking, storage, and other services
A TOS serves as a database for all freight that passes through or is stored in the terminal. Depending on your type of terminal, your TOS must handle all the cargo types you deal with, be they containers of any size, RORO (Roll-On/Roll-Off), or general cargo (dry/liquid bulk, break bulk with different packaging, logs, etc.). Plus, there should be support for IMDG hazardous cargo, temperature-sensitive products, and over dimensional freight.
Many terminals include storage facilities and offer warehousing and/or container freight station services. A TOS allocates storage space and tracks cargo movement within the terminal. A common way to monitor freight is implementing RFID technology that automatically identifies and tracks tags attached to cargo items and then sends information to the TOS database (you can read more about tracking technologies in a dedicated post).
Some ports also provide additional cargo-related services such as stuffing and unstuffing, freight consolidation or breaking down, renting out containers, and so on. A TOS helps efficiently manage all these varied operations, from receiving orders to execution to billing.
Gate management: controlling access to terminal facility
A gate management module helps terminal operators coordinate and monitor all the incoming and outgoing vehicles. The vehicle booking feature allows carriers to choose a convenient appointment slot as well as register vehicle, driver, and freight details. So, upon arrival, all the required information is already in the system and the verification process is as fast and easy as can be.
Besides, a well-built, automated gate management system ensures ISPS (International Ship and Port Facility Security Code) compliance mandatory for ports.
Automating gate operations typically involves creating an infrastructure of interconnected elements (though they can also come as separate solutions) that include
- self-service driver kiosks – to go through a paperless self-verification process and access code entry;
- OCR cameras – to identify and register vehicles, license/number plates, containers, and seals;
- RFID scanners – to identify the passing cargo and assist with inventory management;
- automated security barriers – to control vehicle access;
- intercom devices – to enable communication with terminal staff;
- information displays – to receive instructions and other important information; and so on.
All these recognition technologies and management tools work most efficiently when seamless data exchange is established so that the vessel, container, vehicle, and traffic data are easily shared between modules and collected for further use (reviewing traffic events, analytics, etc.).
Financial and reporting modules: supporting billing and analytics
Managerial activities take place behind the scenes, but are of the same importance as others. A multi-currency billing module allows terminal managers to capture all the billable terminal operations, create accurate invoices, control revenue streams, and efficiently handle flexible tariffs and rates.
Meanwhile, customizable reports and access to robust, data-based analytics give a full picture of facility performance and help make efficient strategic decisions. TOS allows users to export and share reports in a number of standards (XML, CSV, PDF, etc.). Also, TOSs offer a range of access levels to support security.
Additional feature: rail management
If your terminal has an adjacent rail facility as a component of an intermodal supply chain, you need rail management functionality to plan train loading/discharge sequence, schedule resources, and handle other rail-related operations.
TOS integrations
We mentioned earlier how important data sharing is for such a complex system. Now, let’s look a bit deeper into the key TOS integrations that have to be established for efficient terminal performance. But first, let's talk about how these integrations can be built.
EDI vs API
As we mentioned above, Electronic Data Interchange or EDI technology is traditionally used in the maritime industry to exchange information on cargo movement between ports, shipping lines, and other parties. EDI enables data transfer directly between systems; otherwise, it would’ve been done in paper form, through phone calls, or via emails – and take forever.
The two main EDI standards are UN EDIFACT (common outside the US) and ANSI (common in the US). EDI helps exchange such crucial documents as
- bills of lading,
- customs manifests,
- loading/discharge orders/confirmations,
- stowage instructions,
- vessel plans, and much more.
Such automatic document sharing is convenient and has become an industry standard, so all modern TOSs have EDI message processing functionality. However, this format has been there for decades, so now some of the major carriers including Maersk, CMA CGM, and MSC are moving toward newer integration methods – via APIs and using JSON messaging format.
One of the modern data sharing platforms gaining popularity in the maritime industry is TradeLens accessible via a set of REST APIs. It’s underpinned by blockchain technology that ensures data security and is designed to enhance collaboration across global supply chains. For example, carriers can share their position, ETA, electronic bills of lading, and detailed cargo data so that terminals can plan their operations, while shippers, brokers, and consignees can easily track their shipments.
Besides external integrations, APIs are catching on for connecting internal systems that we’ll talk about right now.
Internal integrations: GOS, RTLS, reefer monitoring, and others
Again, there’s no universal rule for all terminals since all of them are different and have distinct operational models and tech ecosystems. Here are just some of the opportunities to connect internal software systems. Note that many of them involve creating a complex Internet of Things (IoT) infrastructure with multiple sensors, smart devices, and connected software to process data.
Gate operating system (GOS). If you have a standalone GOS, connecting it (and all of its sensors and modules such as cameras and RFID scanners) to your TOS will let land carriers receive information about incoming vessels and register their vehicles and loads, while you’ll obtain complete data about the vehicle flow.
Real-time locating system (RTLS). Terminal handling equipment has to be tracked, which is performed with such technologies as GPS, DGPS, RFID, Bluetooth, and so on. The RTLS is a network of tags or wireless transponders attached to equipment units, plus readers installed in different terminal areas to receive tag signals and detect their location.
Reefer monitoring system. If you operate a container terminal, you probably deal with refrigerated/frozen cargo, which requires constant monitoring. Integrating reefer monitoring to have all the information about such temperature-sensitive freight in your TOS is nothing but convenient. Read more about cold chain logistics and how to manage it in our dedicated post.
Radio/mobile data terminals (RDT/MDT). Various technologies are used to create wireless networks in terminals that basically connect workers in the field with a control operator. Handheld, static, or vehicle-mounted devices allow terminal personnel to receive instructions from a TOS and enable communication.
Financial, business intelligence, and general ledger systems. You might use a separate business management solution (say, an ERP such as SAP, Microsoft Business Central, or Oracle) to manage your back-office operations including accounting, analytics, reporting, sales, marketing, and so on. Connecting it to your TOS is crucial for seamless information exchange.
External integrations: shipping lines, freight brokers, tracking data providers
As we said, to synchronize operations and exchange information, terminals connect to shipping lines and freight brokers, usually via EDI – or TradeLens for the most advanced companies. This way, maritime carriers inform ports of their visits and freight, shippers/brokers book empty containers, and terminals confirm booking, loading/unloading operations, and much more.
Another common external connection that terminals take advantage of is the AIS data feed we mentioned above. Real-time ship positions and other marine information is vital for vessel and freight tracking, accurate ETA forecasting, and enhanced berth management. Some of the popular providers with well-developed APIs are MarineTraffic, Vessel Finder, or AISHub.
Popular TOS providers
We don’t promote any of the TOS providers but want to give a brief overview of the most popular products on the market to give you an idea of existing options.
TOS providers comparison
Navis: an array of products for every need
Navis is the industry-leading tech provider of logistics products for terminals, vessels, and even rail operators. Their TOS portfolio includes
- Octopi TOS – a cloud-based solution for small and medium-sized container and mixed cargo terminals that covers all the necessary workflows (gates, yard, billing, etc.);
- N4 TOS – a full-fledged platform for container terminals of any size that offers a suite of handy apps (e.g., Reefer, Lashing, Twistlocks) and optimization modules (Expert Decking, PrimeRoute, Vessel Autostow, and Rail Autostow);
- N4 as a Service – an innovative, cloud-based system that “includes all the capabilities of N4 without the associated costs and complexities of deploying, maintaining and managing it”;
- Master Terminal (originally developed by Jade Logistics)– a highly customizable, multi-modular TOS for mixed cargo ports that supports a broad range of freight types including bulk, break bulk, project cargo, RORO, and container cargo.
As you can see, Navis offers a variety of solutions and services for different needs. The company has been on the market for 30 years and its products are used by almost 300 terminals worldwide. The users’ reviews prove that it’s a great platform to increase operational efficiency, optimize asset utilization, improve safety, and get better business results.
Crane analytics dashboard in Navis N4
CARGOES: a suite of next-gen logistics products based on machine learning and IoT
CARGOES by DP World is an industry-recognized name with a portfolio of logistics products and services catering to various global trade parties, i.e., freight forwarders, customs, importers/exporters, and so on. The Ports&Terminals solutions include
- TOS+ is a management system for container terminals of any size with support for container freight stations, inland depots, and more;
- GC+ is a digital solution for managing multiple types of general cargo;
- IOT+ is a network of smart devices and connected software that offers full, real-time visibility on the microlevel and improves asset management, planning processes, and decision-making;
- AVA+ is a video analytics software to support OCR operations; and more.
CARGOES implements such innovative techniques as deep learning for image recognition and digital twins for environment simulation and visualization. They heavily rely on business intelligence and KPI monitoring for performance optimization and develop machine learning models to enhance analytics.
To support external integration, they have developed a set of APIs.
CARGOES products can be hosted either on-site or in the cloud.
CATOS: all-in-one, user-friendly solution
Total Soft Bank Ltd.'s CATOS (Computer Automated Terminal Operating System) has three modules that cover all terminal operations:
- CATOS Planning helps schedule berth, yard, and vessel-related operations as well as manage human resources.
- CATOS Operation monitors and controls all operations in real-time, whether in the yard, warehouse, at the gate, or elsewhere in the terminal.
- CATOS Management supports billing, reporting, and analytics workflows.
CATOS interface
Besides the convenience of managing all business activities through one system, users are happy with CATOS customization options, intuitive interface, and customer support.
TBA Group: optimizing terminal and warehousing operations
TBA Group specializes in automation solutions for ports, warehouses, and industrial plants. Autostore TOS is a management software designed for container terminals, while CommTrac TOS helps run bulk and break bulk cargo facilities. Whether installed on-premises or in the cloud, these platforms help with yard, freight, and asset management. They also include a vehicle booking system, dynamic vessel and rail planning modules, and billing functionality.
In addition, this provider claims to be able to “integrate seamlessly with all third-party business ERP systems” and provides a range of implementation, testing, and training services.
RBS: robust container terminal solutions and a number of optional modules
RBS (Realtime Business Solutions) develops state-of-the-art software applications for the Container Handling Industry. Their TOPS Expert Enterprise is a traditional on-premises platform and TOPS Expert Cloud can be implemented on a pay-as-you-go model. Both of them are packages of management and optimization modules aimed at handling various terminal operations, from gate to billing.
TOPO, TOPS, TOPX offerings
Moreover, there’s a list of optional modules that can be obtained independently to enhance separate workflows (e.g., reefer monitoring, container freight station, truck appointment, etc.).
There’s also a TOPS KPI dashboard which is an additional remote management, data analysis, and data mining tool to measure and track facility’s performance.
How to choose a TOS? What to consider beyond core functionality
Whatever way you choose, you always have to balance the price with the end result, i.e., the functionality scope that you get. In addition, we have several important considerations on what a great TOS should have.
Mobile-friendliness. It’s crucial to have access to your software from any device, especially for field staff.
Range of freight types. If you operate a mixed cargo terminal, make sure the TOS supports all the freight types you deal with.
Multi-terminal support. This feature is needed for operators that manage several terminals and want to have all their activities in a single system.
Scalability and customization opportunities. You’ll have to customize your TOS anyway because even if you decide to build your own product, your operations might change as you grow and develop. So make sure your system is flexible and allows for adjustments within an acceptable budget and time frame.
Data security, safe storage, and replication technologies. You deal with massive amounts of supply chain data every day, so it’s important that no leakages happen. Information has to be stored safely and backed up with auto-replication technologies – just in case.
Customer support, implementation, and training. If you choose to partner with a TOS provider, make sure you have deep cooperation. They have to fully understand your objectives, challenges, and requirements, work on customization, and guide the entire hardware/software implementation and integration processes.
After that, complete training has to be conducted for all the terminal staff (extra tip: Look for user-friendly software with an intuitive interface for a shorter and easier training process). And last but not least, make sure their customer support is always available and responsive to your requests and queries.
Buy, build, or modernize?
There’s a variety of ready-made solutions on the market but there are two other options of getting a TOS. To build a customized platform from scratch, buy an off-the-shelf solution, or modernize legacy software – the choice depends on your needs and resources.
When to build? If you want a fully tailored product to seamlessly fit into your workflow, develop your own proprietary system, but remember that such a massive project might take years and require significant investment.
When to buy? If, after exploring the market, you understand that existing products can cover your needs with minimal customization required, go with it. Note though, that you’ll still have to fine-tune the system and integrate it into your existing tech ecosystem.
When to modernize? If you have legacy software that works but uses outdated technologies or lacks the functionality you need, you might want to launch a gradual modernization project. In this case, you don’t have to stop your operations but will be able to improve your system one step at a time. Read more about legacy technologies modernization approaches and techniques in our post.
As a final piece of advice, we recommend you make the most of modern technologies like machine learning that will enhance your planning, analytics, and decision-making process. Yes, it comes at a price, but the world today operates on data, so whoever harnesses its power – will gain an unbeatable competitive advantage.
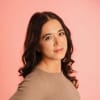
Maria is a curious researcher, passionate about discovering how technologies change the world. She started her career in logistics but has dedicated the last five years to exploring travel tech, large travel businesses, and product management best practices.
Want to write an article for our blog? Read our requirements and guidelines to become a contributor.