Nowadays, even though there is a bunch of small changes you can implement to optimize the work of your warehouse that would be of value in the long run, warehouse management is normally carried out with the help of the warehouse management system (WMS).
Part of the logistics management system we discussed before, and a common integration to a transportation management system, WMS is the software designed to manage, control, and optimize all the processes in a warehouse -- from receiving and storing goods to billing and creating reports. In this article, we talk about the main challenges faced by the supervisors of warehouses, solutions offered by different WMS, and some of today’s top providers in this industry.
The key warehouse processes
To better understand the issues of warehouse management, let’s take a brief look at its main processes. The six fundamental warehouse processes include receiving, putaway and storage, picking, packing, shipping, and returns.
Main warehouse processes
Receiving involves control over the delivery to your warehouse of the correct quantity of the desired product - of the right quality at the right time. This process can in turn be broken into smaller ones:
- placing a purchase order,
- preparing space in the warehouse,
- unloading (manual or automated),
- verification,
- filling in the database, etc.
At this stage automated dimensioners that capture cargo measurements can be helpful as are dock schedulers to ensure that an adequate number of workers are on hand.
Putaway is delivering goods to the optimal place in the warehouse. Here the correct identification of each SKU (stock keeping unit) and getting it to the most relevant spot is important. Storage conditions also matter to ensure the safety of goods and employees. Slotting and space management techniques as well as overall warehouse design are critical to streamlining these operations and using space most effectively.
Picking is the process of collecting goods from the storage place according to the customer’s order. It is thought of as the costliest, most time-consuming, and most error-prone. Here, mobile scanning devices and voice systems can save tons of time and reduce errors significantly. It’s also worth considering adopting one of the picking methodologies, such as cluster picking, zone picking, wave picking, etc.
Packing is putting the ordered items together, checking their quality, and getting the product ready for shipment. At this point, it’s important to have all the necessary data on the order and also the type/amount of packing material required for each order. Automatic wrappers can also reduce time spent and packing material used.
Shipping or dispatching is sending goods to the customer and making sure they are delivered safely and on time. Here, again, proper scheduling, labor management, and tracking systems are key to satisfying customer demands.
Returns is something most companies wish would never happen, but unfortunately, they are also a part of the game, especially for eCommerce. About 5 to 10 percent of in-store purchases are returned, but that rises to 15 to 40 percent for online purchases, according to David Sobie, cofounder and CEO of Happy Returns. Obviously, managing returns and refunds is a hassle and requires special attention. Returned units have to be properly identified, sorted, and dealt with, whether it is by putting them back on the shelf, sent to repair, discarded, returned to the manufacturer, etc.
Now that we've described the key processes that happen at the warehouse, let's talk about how warehouse management software works and how it matches these processes.
What is a warehouse management system?
Traditional order management systems (OMS) or enterprise resource planning (ERP) systems have basic warehousing functionality, but many companies soon find that they have outgrown their capabilities. So, the main advantage of the WMS is that it covers other aspects of the supply chain besides inventory and order management - such as labor management, financial management, reporting, and more.
Obviously, every business is unique and will have different software requirements. Let’s take a look at the main modules most WMS platforms have and the most common problems they help to deal with.
Relation of warehouse processes and WMS modules
Inventory management
Creating purchase orders. WMS stores all your suppliers’ information in one place and syncs it to actual inventory levels making it easy to manage procurements. The product can also be added to the order by simply scanning the barcode. The orders are then emailed to the supplier right from the system.
Receiving and Putaway. Scanning devices integrated with WMS optimize receipt and direct workers to the best location to shelve the product. WMS may also suggest multiple strategies for slotting and best usage of the storage space depending on the type and characteristics of goods you deal with. For example, fast-selling products have to be put in the most accessible areas; fragile, in those areas where potential for damage will be minimized; perishables, according to their storage requirements and expiration date; and so on. Location recommendations are also connected to the forecasting module and are based on trends and product demand.
An example of warehouse layout design
Storage and tracking. Location control is the core of warehousing, especially if you work with completely different types of goods or have to handle stock for multiple clients. Being able to track the exact location of every single SKU prevents pilferage and helps optimize further order processing. If you still have trouble locating goods in your warehouse or deal with high-value items, consider adding a real-time locating system (RTLS) to your WMS to enhance the tracking accuracy. Also, storage conditions are vital for some product categories like perishable food - WMS keeps track of expiration dates and shelf life and prioritizes products accordingly.
Stock level control. WMS helps monitor the amount of product in multiple warehouses, notifying users if the level is too low and needs replenishing. Automatic reordering can be set up as well to prevent total stock depletion and overselling. Cycle counting is another great tool for inventory control and is offered by most WMSs.
Order management
Processing customers’ orders is the key function of any sales-oriented business. Accuracy and speed are crucial to achieving customer satisfaction. There are many ways how implementing WMSs can help improve efficiency and reduce errors on every stage of this complex process.
Receiving/creating sales orders. If you work with various eCommerce platforms like Magento or Shopify and marketplaces like Amazon or eBay, integrating them with your WMS will allow you to manage all the orders from different channels in one system. Also, since most of the WMS are cloud-based, orders can be created on the go right from the mobile device, i.e., at trade shows or sales meetings.
Picking. Picking lists can be a pain to create. WMS will let you sort and print lists conveniently, e.i., by bin location, order date, SKU, etc. Mobile devices or voice systems can then guide workers to the exact place where the product is stored. If multiple items have to be picked, the optimal route together with the necessary equipment will be suggested to reduce travel time. Barcode or RFID scanners ensure the accuracy of getting the right items. Today, big players like Amazon or Alibaba also use robots in their warehouses and implement other AI technologies.
Using mobile scanning devices
Packing. The type and amount of packaging are calculated automatically for every order and optimal packing procedure is suggested (e.i., gift wrapping). The shipping labels for UPS, FedEx, and USPS (as well as price tags, logos, BOLs, and other necessary paperwork) can be printed directly from the system so there is no need to manually enter addresses or retype tracking numbers. Quality control is also simplified as employees have the exact information and standards for every item.
Shipping. Rate calculation and real-time parcel tracking are available in most WMSs. If multiple orders are shipped to the same address, they can be merged to reduce shipping costs. Features of cross-docking and drop shipping are also offered by some providers.
Returns. WMS can help streamline this unpleasant process by automating every step: creating the return, recording the reason, updating stock, issuing full or partial refunds, and generating reports.
Invoicing. Invoices are created and sent automatically, including individual discounts and payment options for every customer. Normally multiple formats are supported, whether it is email, CSV, or EDI.
Overall, organizing your orders in one central system provides full visibility of the complete history for every order - payment information, shipping status, staff involved, total time spent, etc. Moreover, giving your customers access to view and manage their own orders increases their engagement and trust and encourages future cooperation.
Labor management
When the company is still small and you just have a handful of employees, managing is easy. Scheduling, payrolls, and performance control can be done manually and don’t take long. However, it becomes more complicated as the company grows and the staff becomes more numerous. Most WMSs offer some kind of a labor management module that can be handy for:
Scheduling. For example, sometimes more people are needed at the docks to unload the incoming shipping quickly and not let the product overstock dock areas, and at other times a big order needs to be collected and packed promptly. Seasonal peaks and valleys also strongly affect labor demand and allocation. Automated schedulers help plan and forecast the exact number of people needed by day, zone, and job type according to your procurement and shipping schedule.
Increasing performance. Tracking KPIs (i.e., the number of items picked, number of orders packed, travel time, etc.) keeps managers informed, rewards stronger workers and identifies those not meeting their requirements or needing additional training. Moreover, workers’ engagement increases due to visibility and access to operational results and peer comparisons.
Manhattan WMS employee engagement progress screen, source
Safety control. Unfortunately, since theft is a common problem, installing cameras and sensors and implementing video surveillance has become a widespread solution. Integrating a security system with your WMS helps monitor what exactly is happening in the warehouse by tracking staff location, identifying license plates of the incoming trucks, limiting access to certain areas, etc.
Overall cost estimation. Breakdown by process, employee, shift, supervisor, department, or customer provides full cost visibility and points out which customers are unprofitable to work with.
Financial management and reporting
Monitoring business performance and sales trends across locations, customers, and products is mandatory for making informed, data-driven decisions about future actions and developments. WMS offers numerous opportunities to track and generate reports concerning every side of your business:
- Customizable metrics let you assess all the data and know your most profitable customer, top-selling product, best-performing sales channel, most efficient worker, peak sales season, etc.
- Automatic balance sheet accounts for revenue, taxes, and the cost of products sold based on real-time data saves time and minimizes miscalculations. Many WMSs support multi-currency pricing, different tax systems, and landed cost management, which is crucial if you operate in multiple locations.
- Integration with accounting platforms like QuickBooks or Xero is also a common feature to have all accounting in one place.
Logiwa WMS integration options
You can learn more about performance monitoring from our inventory management KPIs post since many of them are related to warehouse operations.
Risk Management and Forecasting
Risk analysis and comprehensive planning are key to successful company development. Modern software offers solutions to analyze operational data and create forecasts, taking into account possible risks or actually disruptions in progress. A demand planning feature ensures that there is no overstocking and no products are going to waste as well as preventing stockouts. Products that are seasonal or selling fast can be tracked and prioritized. Full visibility and structuring of data helps better understanding and predicting customer behavior and needs.
Top providers of WMS
Most WMS software providers will offer a basic set of features such as:
- barcode and RFID scanners compatibility,
- providing real-time data streaming,
- inventory location recommendations,
- picking and packing options,
- product tracking,
- warehouse layout planning,
- kitting,
- creating reports,
- billing and invoicing,
- integration with ERP and other software,
- customization opportunities,
- on-Cloud basis, etc.
However, when you do deeper exploration, it turns out that all software options have specific weaknesses and strengths, no WMS on the market is absolutely perfect, and different WMS suit different purposes. Providers can focus on a certain business sector (wholesale, retail, or manufacturing) or company size (small, medium, or large). Below are descriptions of some of the top-rated WMS providers.
WMS providers’ comparison
Fishbowl Warehouse - best value for money
Fishbowl has its primary focus on the balance of usability and affordability. It offers multiple features for small and midsize companies to help manage inventory.
- Paper documentation is minimized by using mobile devices for scanning products, managing stock, and creating invoices.
- You can track inventory movement between multiple locations, get real-time updates, study sales trends on a warehouse-by-warehouse basis, and obtain inventory requirement predictions.
- It perfectly integrates with QuickBooks, Xero, Magento, Salesforce, UPS Ready, and other business solutions. Thus, you don’t have to manually enter your inventory or any other data into your accounting system.
- Fishbowl has over one hundred report options plus you can request a custom one.
- It is reported to be very user friendly having a basic interface that is quite easy to master.
Pricing starts from $4,395 for a one-time fee and depends on the number of user licenses you need, making it comparatively affordable, considering that there is no monthly fee.
Fishbowl is not perfect though. For instance, it does not support cross-docking and many users reported having a hard time fixing mistakes (no “undo” button). Also, every custom feature has an additional charge.
Fishbowl Order management interface
Manhattan WMS - best for fast-shipping
Manhattan is a flexible warehouse management solution popular among 3pl operators and is voted the best choice for fast shipping. Created for medium and enterprise-sized companies, it’s perfectly compatible with mobile devices and provides lots of fulfillment methods to speed up the flow of goods and organization data. Besides the expected inventory control and billing solutions, other features include:
- arranging multi-carrier deliveries, i.e., using multiple logistic providers to move your goods helpig you choose the fastest or cheapest solution;
- cross-docking support;
- order streaming, which involves synchronizing and prioritizing orders;
- boosting productivity and engaging employees by using gamification techniques;
- optimizing the warehouse layout for easy picking and packing;
- creating material handling policies and standards to ensure all workers know the processes and operations with inventory;
- accommodating omnichannel and/or multi-tenant fulfillment;
- appointment scheduling and yard management;
- handling multiple companies with different operating standards and rules within the same facility; and
- constantly providing managers with overall operational data allowing to react immediately if needed as well as forecast and plan ahead.
However, since the program is such a large and multi-component one (and more expensive than most other platforms), it might not be the best option for smaller businesses. It can also be challenging to implement and master all the functionality it suggests. Besides, this software might not be as functionally fulfilling for retail store operations as some of its competitors.
Manhattan WMS Facility Console
NetSuite WMS (by Oracle) - best for perishables
NetSuite is capable of managing core business processes from a single system and is well suited for inventory management and production management. It was voted a great choice for manufacturing and distribution companies. NetSuite has all necessary features to streamline warehousing operations and ensure on-time delivery, including:
- a solution for tracking perishables that involves monitoring expiration dates and shelf lives, and prioritizing specific items;
- compatibility with various scanning devices that direct putaway and picking;
- setting material handling policies;
- real-time monitoring of labor productivity and KPIs through user dashboards; and
- various customizable tools for financial management - accounting, reporting, analytics, payments, billing, etc.
Netsuite provides big opportunities for customization, but they are pricey and at times difficult to implement and maintain (e.i., the payroll module is not fully integrated into the product but outsourced to a third party). Also, many users were not happy with the support services and warned about tricks in the contracts and unexpected price increases.
It can be a comprehensive solution for a midsize or enterprise company to handle all the scope of ERP and WMS operations. For a small business, however, the investment, customization, and steep learning curve are not worthwhile.
NetSuite Accounts receivable dashboard
QuickBooks Commerce (formerly TradeGecko) - best for eCommerce
QuickBooks Commerce is a powerful eCommerce platform for multichannel and wholesale businesses specializing in B2B sales. It offers:
- multiple inventory control and inventory tracking features;
- seamless integration with Amazon, Shopify, WooCommerce, Magento, ShipStation, etc., and multichannel sales management;
- demand forecasting and purchase order generation;
- invoicing tools with built-in credit card payment options;
- customer insights, reports, and forecasting;
- multiple catalogs and price lists with individual discount options, multiple currencies support; and
- user-friendly interface.
This product seems to be a great piece of software for modern online businesses of any size. Most customers are happy with using it, mentioning only minor drawbacks like inconvenient printing layouts, limited language choices, or imperfect dropdown menus.
QuickBooks Commerce sales report interface
3PL Warehouse Manager - best for 3PL companies
3PL Warehouse Manager is a completely cloud-based WMS designed exclusively for third-party logistics warehouses that helps manage multiple customers, processes, and billing schedules. Besides automating daily routine operations, it also:
- enables access to real-time information and provides global visibility of stock and processes in the warehouse;
- has an easy-to-use, intuitive design;
- provides customized user access security levels, i.e., allows users' customers to view and manage their orders and inventory on their own;
- has FedEx and UPS integration;
- offers a billing automation module that allows to track operational costs and all the activities on a per-customer basis;
- links EDI partners to shipping providers and e-commerce platforms, enabling communication with their network via the cloud; and
- offers appealing price options, especially considering that no hardware or software is needed.
The provider offers a demo version on the official website and prices are calculated according to individual company requirements. Training and support are available according to the options chosen.
While users are generally satisfied with the overall functionality of the platform, some mentioned poor forecasting options, no cross-docking solution, and also limited KPI and metrics to assess daily performance and create full-fledged reports.
3PL Warehouse Manager Customer management page
What to consider when choosing a WMS
It is obvious that benefits and savings from the implementation of a WMS can be significant as they enhance performance and streamline all the activities in the warehouse to speed up operations and reduce errors. Companies that are not currently using a WMS solution are likely to see an ROI (return of investment) within six to twelve months.
In choosing the best WMS provider, you have to be extremely cautious and detailed, taking into account not only their software capability, functionality, and price, but also such factors as:
Desired integration options - besides integrating new and legacy software and technologies you are already using, you might also need to integrate with various marketplaces, shipping partners, other stores, warehouses, etc.
Mobile-readiness - this quality involves being accessible, legible, and usable to visitors across all mobile devices like tablets and smartphones.
Customization options and cost - the adopted software should be capable of being modified to fit your unique needs.
Flexibility and scalability - the chosen solution must be able to adapt to the growing needs and requirements related to company development.
UI and time necessary to educate staff and/or change the configuration if needed.
Capability of handling and managing other areas of operation besides warehousing itself, e.i. shipping, labor management, finance and reports, etc.
According to the 2020 MHI Annual Industry Report, 20 percent of supply chain leaders believe that the digital supply chain is the dominant model right now and 80 percent say that it will be the industry’s dominant model within the next five years. So, if you are looking for a perfect time to invest into technology and make your warehouse perform with maximum efficiency - now is that time.
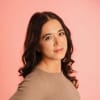
Maria is a curious researcher, passionate about discovering how technologies change the world. She started her career in logistics but has dedicated the last five years to exploring travel tech, large travel businesses, and product management best practices.
Want to write an article for our blog? Read our requirements and guidelines to become a contributor.